PET preforms are a cornerstone of the packaging industry, serving as the essential building blocks for producing plastic bottles. From water and soda bottles to containers for pharmaceuticals and cosmetics, PET preforms are ubiquitous in modern manufacturing. This article delves into every aspect of PET preforms, providing a comprehensive guide for manufacturers, suppliers, and industry enthusiasts.
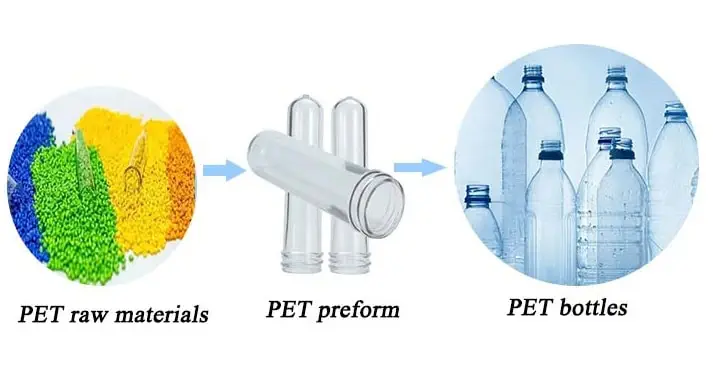
What Are PET Preform?
PET preforms are intermediate products made from polyethylene terephthalate (PET), a versatile and durable plastic. Shaped like test tubes, they are designed to be reheated and blow-molded into the desired bottle shape. PET preforms offer a cost-effective and efficient solution for producing high-quality plastic bottles.
Their design ensures uniformity, strength, and recyclability, making them a popular choice for packaging applications worldwide.
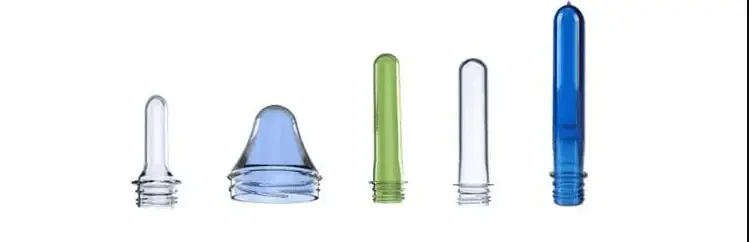
Applications of PET Preform
PET preforms are used across various industries, including:
- Beverage Industry: PET preforms are transformed into bottles for water, carbonated drinks, and juices.
- Pharmaceuticals: Packaging for liquid medicines and health supplements.
- Cosmetics: Containers for shampoos, lotions, and creams.
- Food Industry: Jars for sauces, oils, and condiments.
The adaptability of PET preforms ensures they meet the demands of diverse sectors, offering durability and aesthetic appeal.
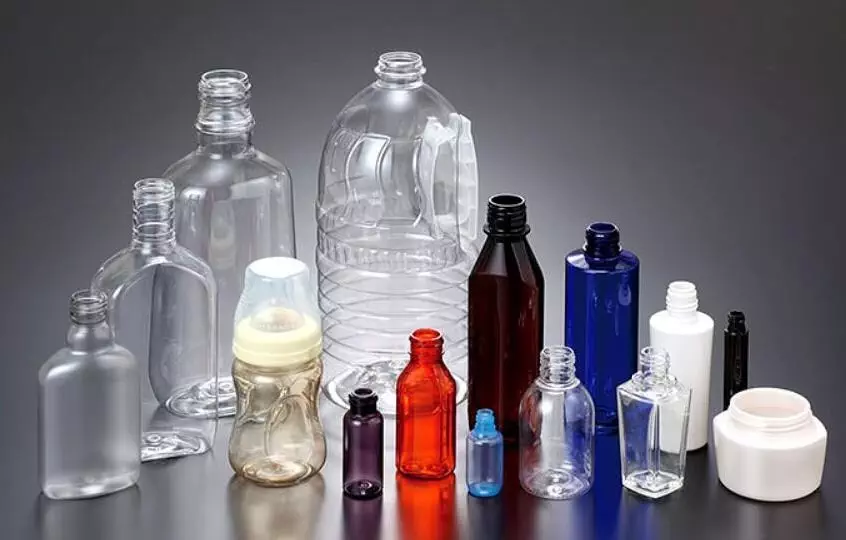
Materials Used in PET Preform Manufacturing
PET preforms are manufactured using polyethylene terephthalate, a thermoplastic polymer known for its clarity, strength, and recyclability. Key characteristics of PET include:
- Lightweight: Reduces shipping costs and environmental impact.
- Recyclable: Supports sustainability initiatives.
- Durable: Resistant to impact and leakage.
These properties make PET an ideal choice for packaging applications where performance and sustainability are critical.
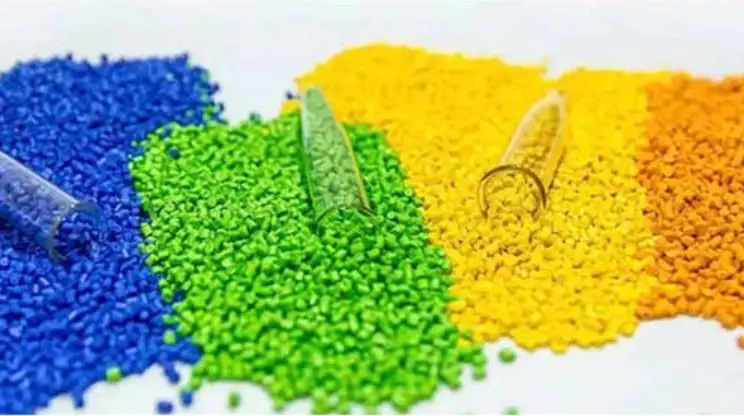
PET Bottle Preforms Manufacturing Process
The production of PET preforms involves several precise steps:
- Material Preparation: PET resin is dried to remove moisture, ensuring a smooth molding process.
- Injection Molding: The dried resin is melted and injected into a preform mold under high pressure.
- Cooling and Ejection: The preform is cooled to retain its shape and then ejected from the mold.
- Quality Inspection: Each preform is checked for consistency, dimensions, and transparency.
This highly controlled process ensures that PET preforms meet stringent quality standards, minimizing material waste and maximizing production efficiency.
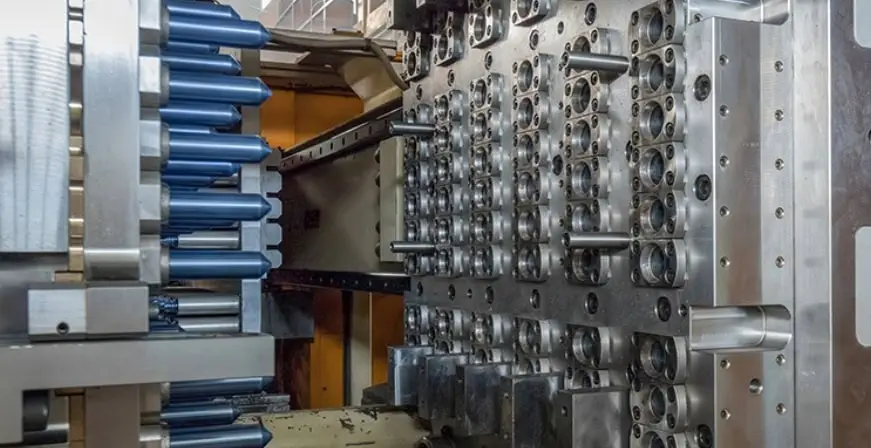
Key Equipment: PET Preform Molding Machine and Bottle Blowing Machine
The manufacturing of PET preforms and their transformation into bottles rely on specialized machinery:
- PET Preform Molding Machines: Used to mold the resin into preforms. These machines are designed for high-speed and precision manufacturing.
- Bottle Blowing Machines: Heat the preforms and blow them into the desired bottle shape. These machines are crucial for ensuring uniformity and strength in the final product.
Advanced machinery integrates automation and energy-saving features, improving productivity and reducing operational costs.
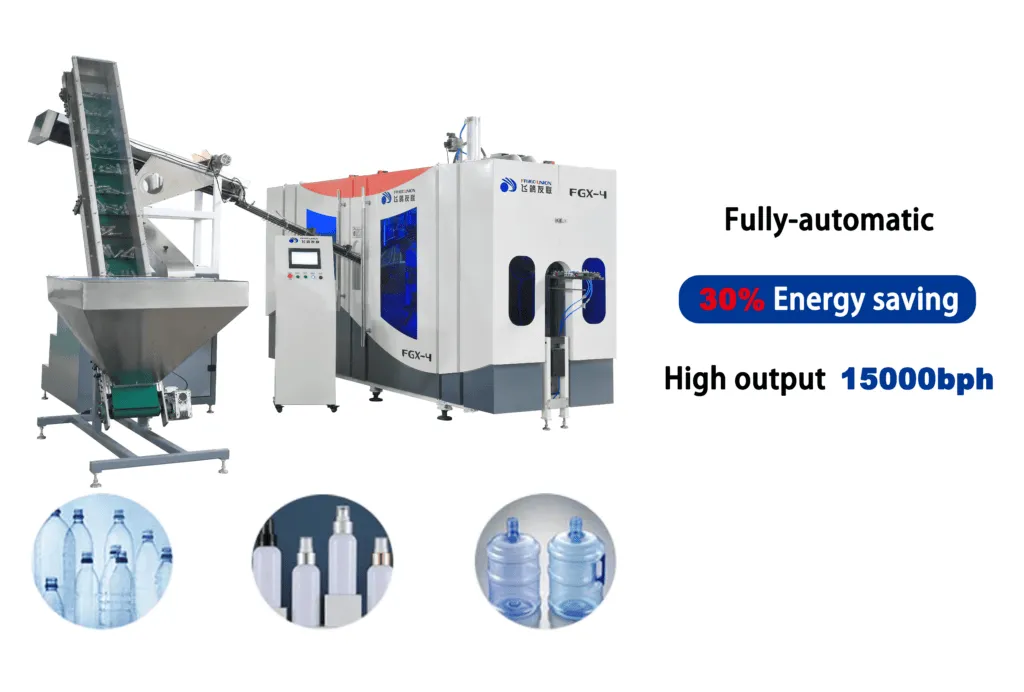
Advantages of Using PET Bottle Preforms
PET preforms offer several benefits:
- Recyclability: PET can be recycled multiple times, reducing environmental impact.
- Cost Efficiency: Preforms are lightweight and easy to transport, lowering logistics costs.
- Durability: Resistant to impact, leaks, and chemical reactions.
- Versatility: Suitable for various shapes, sizes, and applications.
These advantages make PET preforms a preferred choice in the packaging industry.
PET Preforms for Drinking Water and Beverage Bottles
Water bottles are one of the most common applications for PET preforms. When you want to produce plastic beverage bottles or you want to setup a mineral water factory, bottle preforms are a necessityThe manufacturing process for these bottles involves reheating the preforms and blowing them into molds that define the bottle’s shape and size. Quality standards are critical in this application to ensure:
- Purity: No chemical leaching into the water.
- Strength: Withstanding transportation and handling.
- Clarity: Enhancing aesthetic appeal and consumer trust.
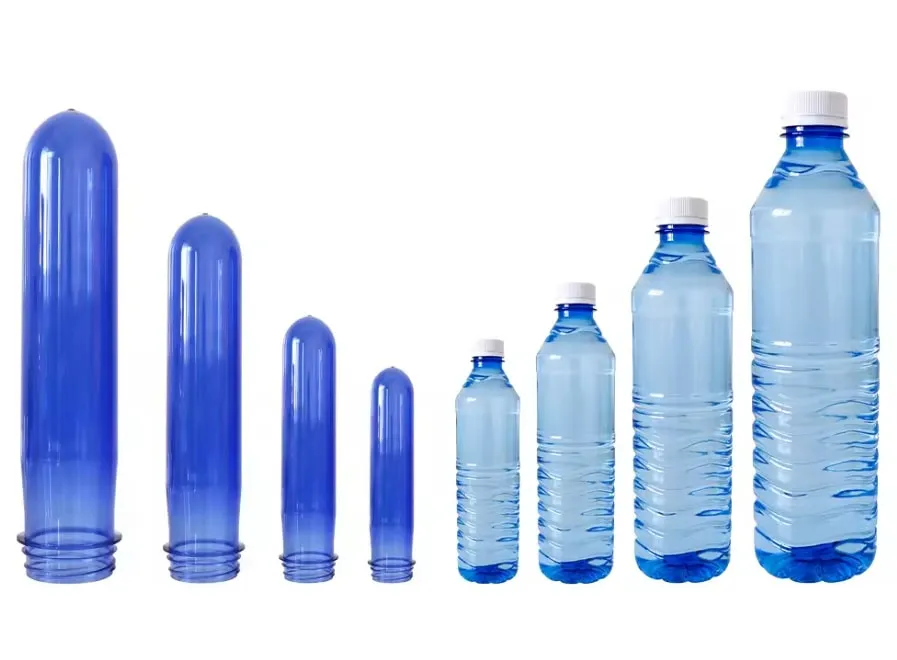
Challenges in Plastic Preform Manufacturing
While Plastic PET preforms are highly advantageous, their production comes with challenges:
- Material Sourcing: Ensuring consistent supply of high-quality PET resin.
- Precision Molding: Achieving uniformity and minimizing defects.
- Energy Consumption: Managing high energy use during molding and heating processes.
To overcome these challenges, manufacturers are adopting advanced technologies, such as energy-efficient machinery and process automation.
Future Trends in the PET Preform Industry
The Plastic PET preform industry is evolving with innovations aimed at sustainability and efficiency:
- Biodegradable PET: Development of eco-friendly materials to reduce environmental impact.
- Advanced Machinery: Integration of AI and IoT for smarter production processes.
- Customization: Growing demand for unique shapes and designs.
These trends are shaping the future of the packaging industry, making Plastic preforms an even more integral component.
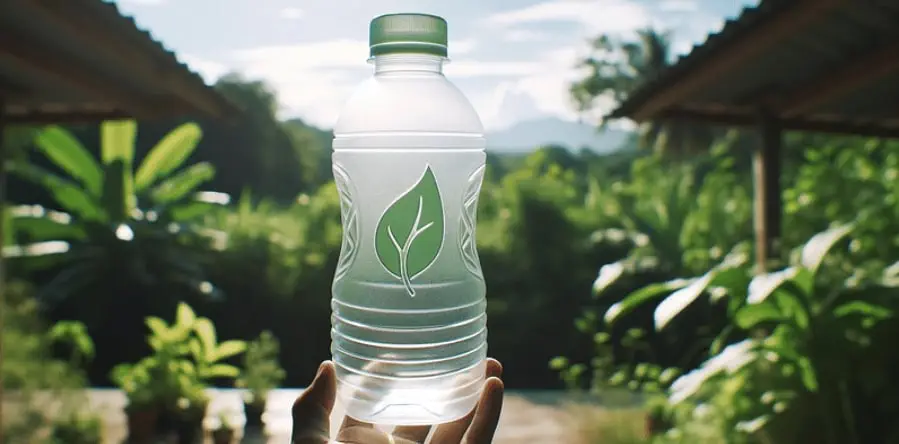
Conclusion
Plastic PET Bottle preforms play a vital role in modern packaging, offering unmatched versatility, efficiency, and sustainability. From their use in water bottles to high-end cosmetic containers, PET preforms cater to diverse needs while supporting environmental initiatives. As the industry continues to innovate, PET preforms will remain a cornerstone of packaging solutions.
Explore the possibilities of Plastic PET preforms for your business today and embrace the future of packaging technology.