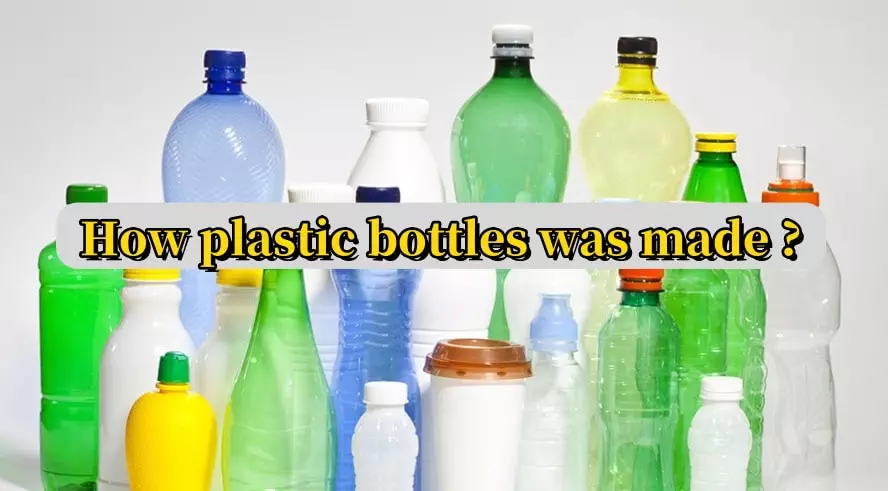
Plastic bottles are an essential part of modern life, used widely in packaging for mineral water,beverages, cleaning products, and personal care items. But have you ever wondered, how are plastic bottles made? This comprehensive guide will explain the materials, stages of production, and technologies involved in the plastic bottle manufacturing process. Whether you’re curious about how plastic PET/HDPE bottles are made or considering starting your own production line, this article has everything you need to know.
What Are Plastic Bottles Made Of?
Plastic bottles are made from a variety of plastics, each selected for its specific properties and intended use. Common materials include:
- Polyethylene Terephthalate (PET): A lightweight, durable, and recyclable thermoplastic polymer widely used for water and soda bottles. PET is derived from a chemical reaction between ethylene glycol and terephthalic acid. Is PET Plastic BPA Free? The Safety of Bottled Water
- High-Density Polyethylene (HDPE): Known for its sturdiness and resistance to chemicals, HDPE is used in milk jugs and detergent bottles.
- Polypropylene (PP): A versatile plastic used in caps and closures due to its strength and high melting point.
- Polycarbonate (PC): Used for reusable water bottles and containers due to its toughness and transparency.
Each type of plastic has unique properties, chosen based on the intended use of the bottle. For example, how water bottles are made requires PET for its ability to preserve freshness, while HDPE is ideal for products like juices and milk. Understanding these materials is key to producing efficient, sustainable packaging solutions.
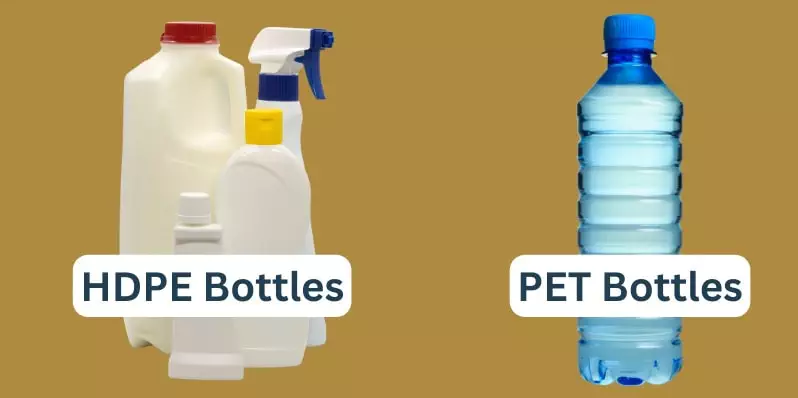
The Plastic Bottle Manufacturing Process
The production of plastic bottles involves several stages, each playing a vital role in shaping the final product. The manufacturing process is flexible, allowing for customization in size, color, and shape to meet specific product needs.
Step 1: Creating the Preform
- Raw plastic pellets (usually PET) are melted and injected into molds using injection molding machines to create preforms.
- These preforms, small and tube-like, serve as the starting point for bottle production.
- Many manufacturers purchase preforms instead of producing them in-house to save time and costs.
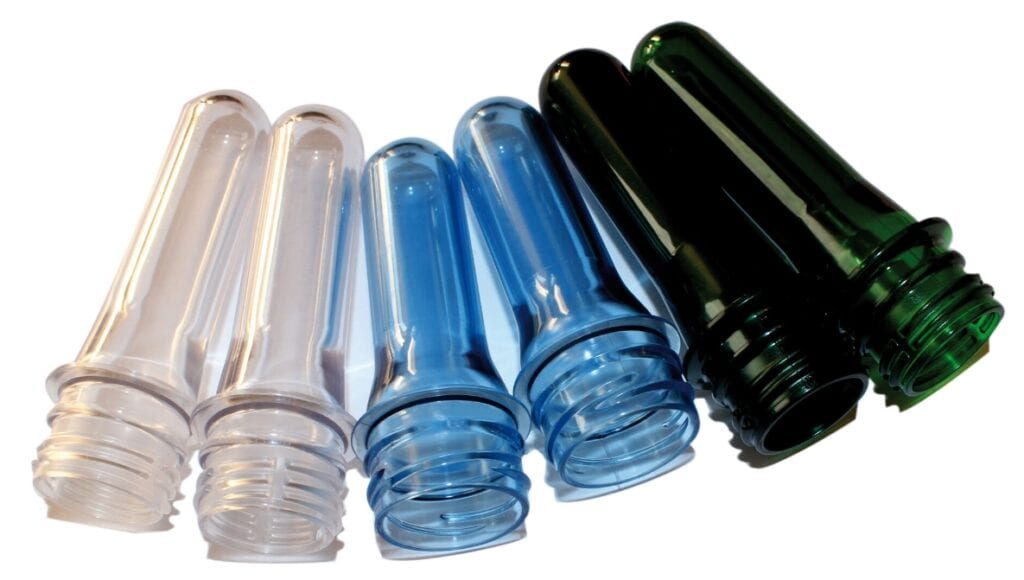
Step 2: Blow Molding
- Preforms are heated to a specific temperature, making them pliable.
- Using Bottle blowing machine, the preform is blown into a mold, forming the desired bottle shape.
- The mold determines the bottle’s size, design, and capacity.
Step 3: Cooling and Solidification
- The newly formed bottles are cooled to stabilize their structure.
- Cooling ensures the bottles maintain their intended shape and strength.
Step 4: Quality Inspection
- Each bottle undergoes rigorous inspection to identify defects like cracks, uneven shapes, or weak points.
- Bottles are tested for durability, resistance to pressure, and chemical safety.
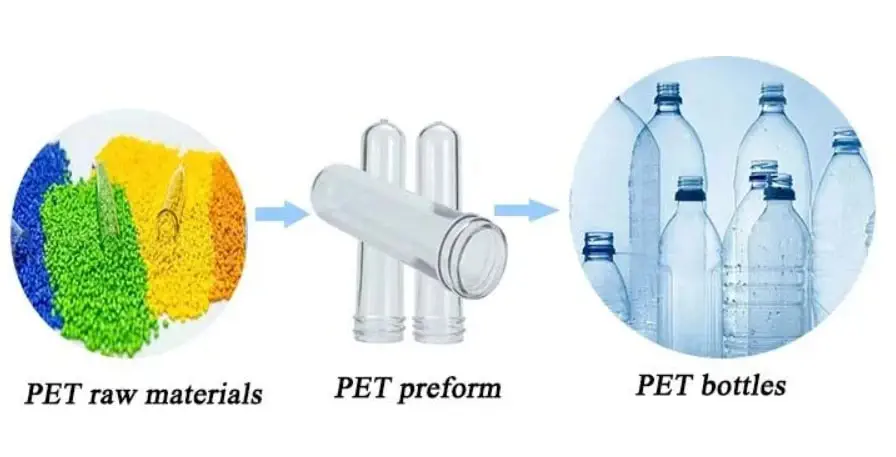
Alternative Manufacturing Methods
Beyond standard blow molding, several other techniques are used depending on the type of bottle and material:
Extrusion Blow Molding
- Plastic pellets are melted and extruded into a tube-like form.
- Compressed air blows the molten plastic into a mold to shape the bottle.
- This method is ideal for producing HDPE bottles for milk, juice, and oil packaging.
Stretch Blow Molding
- Preforms are heated and stretched both axially and radially while being blown into the mold.
- This technique creates strong, lightweight bottles, particularly for carbonated drinks and water.
These alternative methods demonstrate how diverse the water bottle manufacturing process can be, catering to specific product requirements.
Quality Control and Inspection
Quality control ensures that plastic bottles meet the highest standards of safety and performance. Key aspects of this stage include:
- Defect Detection: Bottles are checked for cracks, uneven finishes, and other visible defects.
- Strength Testing: Bottles are tested to ensure they can withstand pressure, especially for carbonated drinks.
- Consistency Checks: Dimensions, weight, and capacity are verified to match specifications.
- Chemical Safety: Bottles are assessed for resistance to chemicals and suitability for food-grade use.
Factors Affecting the Bottle Production Process
Several factors influence the efficiency and outcome of plastic bottle production:
- Machine Efficiency: The type of machinery used, such as a Automatic bottle blowing machine or automatic plastic bottle making machine, directly impacts production speed, cost, and consistency.
- Material Quality: The quality of PET or HDPE resin determines the bottle’s strength, transparency, and recyclability.
- Energy Consumption: Choosing energy-efficient machines can significantly reduce operational costs while maintaining high output.
- Automation: Automated systems enhance precision, reduce labor costs, and allow for higher production volumes, making them indispensable for large-scale operations
Selecting the right equipment and materials is crucial for an optimized production process.
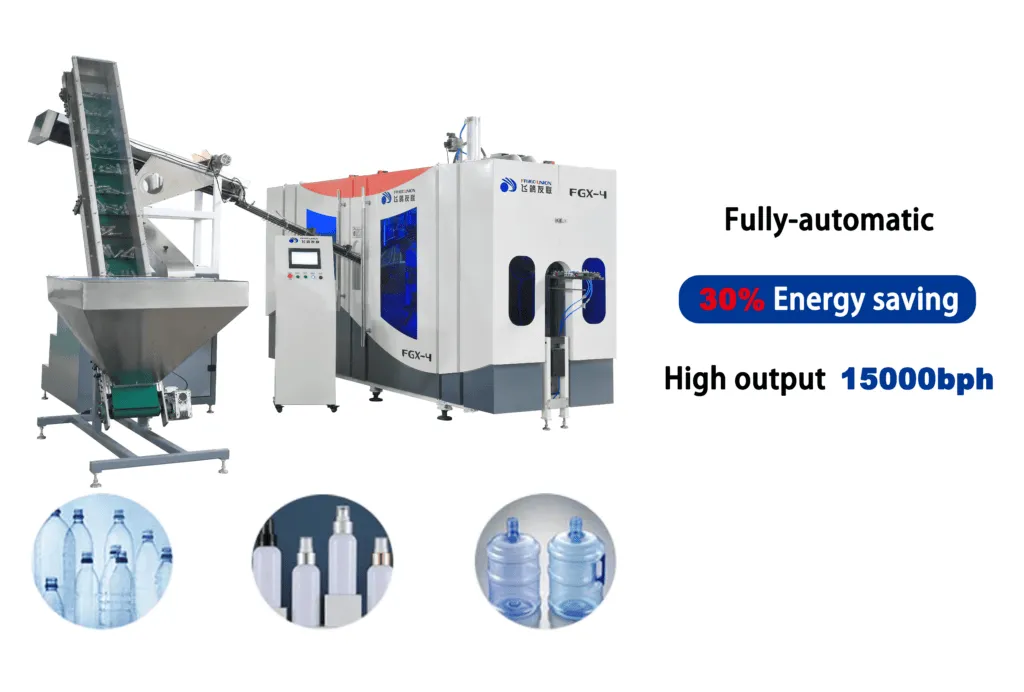
Common Challenges in Plastic Bottle Manufacturing
While the process is highly efficient, manufacturers face several challenges:
- Material Waste: Excess plastic generated during production must be minimized or recycled to reduce waste.
- Environmental Impact: Addressing concerns over plastic pollution is critical. Many manufacturers are investing in recycling initiatives and exploring biodegradable plastics.
- Machine Maintenance: Regular maintenance of blow molding machines ensures consistent product quality and prevents costly downtime.
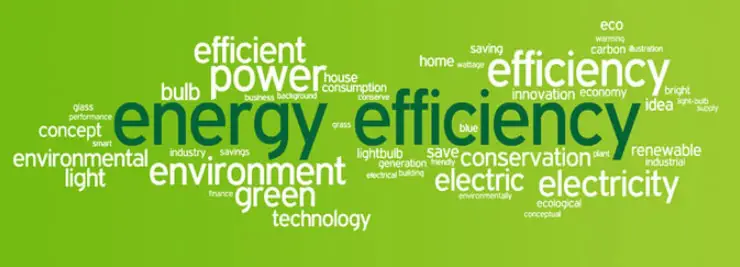
Conclusion on Bottle Manufacturing
The production of plastic bottles is a highly sophisticated process involving advanced machinery and precise techniques. From selecting the right materials to ensuring top-quality manufacturing standards, each step is crucial for producing bottles that meet industry demands.
As manufacturers face increasing pressure to adopt sustainable practices, innovations like biodegradable plastics and energy-efficient machines will likely shape the future of plastic bottle production. For businesses seeking to optimize their production processes, investing in high-quality equipment like blow molding machines is key.
If you’re considering starting or optimizing a bottle production line, explore our newly released 3 in 1 blowing-filling-capping-combiblock machine designed for efficiency and precision. Contact us today for more information!