Automated Guided Vehicles (AGVs) are revolutionizing industries by providing efficient, autonomous transportation of materials and goods within controlled environments. These vehicles operate without human intervention, utilizing pre-defined paths or guidance systems. AGVs are widely used in manufacturing, warehousing, distribution, and a variety of other sectors, helping businesses streamline operations and improve productivity.
What is an Automated Guided Vehicle (AGV)?
An Automated Guided Vehicle (AGV) is a mobile robot that automatically transports goods or materials in facilities like warehouses, factories, and distribution centers. AGVs do not require human operators and follow specific guidance systems that can be either embedded in the floor or powered by wireless technologies. These vehicles are crucial in modern industries for their ability to enhance efficiency, minimize human labor, and improve safety.
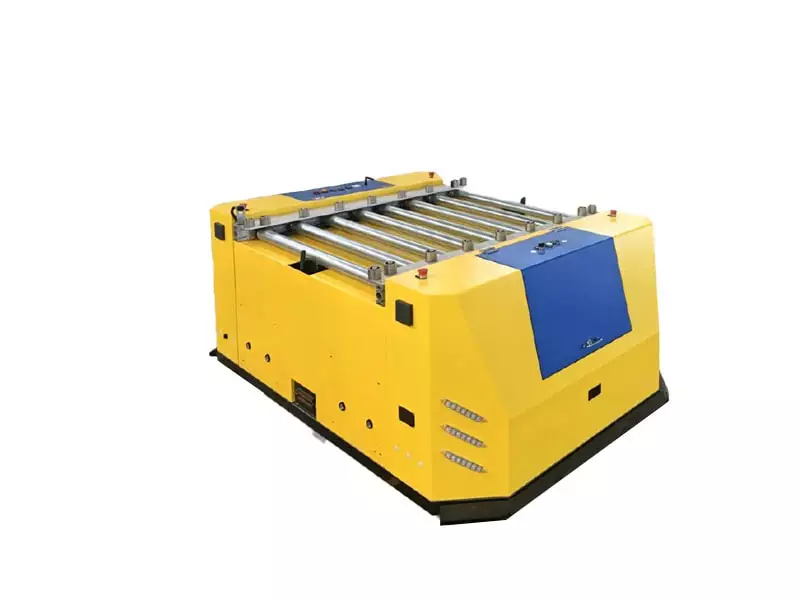
Types of AGVs
AGVs come in various forms, each designed to perform specific tasks suited to different industrial environments. Below are some common types of AGVs:
1. Forklift AGVs
Forklift AGVs are automated versions of traditional forklifts, designed to lift and move materials at varying heights. These AGVs are widely used in warehouses and manufacturing facilities to stack pallets, retrieve items from racks, and load or unload trucks. They offer the flexibility to carry large loads without requiring manual intervention.
2. Unit Load AGVs
Unit Load AGVs are designed to transport individual unit loads such as pallets, containers, and racks. They are equipped with platforms or forks to carry these loads, making them ideal for use in warehousing, distribution, and manufacturing settings. Unit Load AGVs streamline operations by automating the transportation of goods across different stages of the supply chain.
3. Towing AGVs (Tuggers)
Towing AGVs, or tuggers, are used to pull carts, trailers, or other wheeled devices autonomously, similar to a train system. They are equipped with a coupling mechanism to connect and transport loads, and are often employed in manufacturing environments where multiple smaller loads need to be moved simultaneously.
4. Heavy Burden Carriers
These AGVs are specially designed to handle heavy-duty loads, making them suitable for industries like construction and automotive. Heavy Burden Carriers can navigate through tight spaces, and some models offer self-loading capabilities, improving both flexibility and efficiency.
5. Hybrid AGVs
Hybrid AGVs combine both automated and manual operation. These vehicles can operate autonomously following predefined paths but can also be controlled manually when necessary. Hybrid AGVs are beneficial in dynamic environments where the flexibility to switch between automated and human-controlled operations is essential.
6. Autonomous Mobile Robots (AMRs)
AMRs, while similar to AGVs, offer a more advanced level of autonomy. They are equipped with sensors, cameras, and advanced AI software, allowing them to understand and interact with their surroundings in real-time. AMRs are more adaptable than AGVs, able to navigate dynamically and avoid obstacles in ways that traditional AGVs cannot.
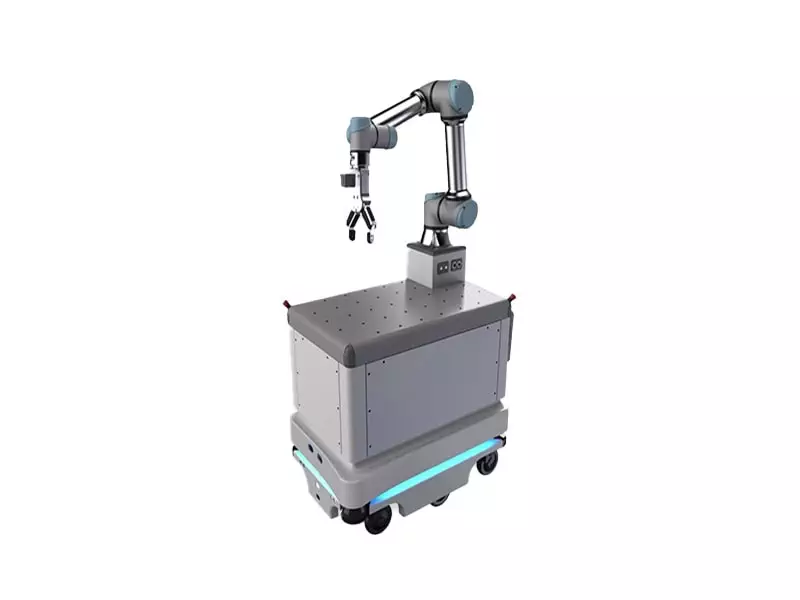
How Automated Guided Vehicles Work
AGVs rely on various navigation technologies and control systems to operate autonomously within their environments. These technologies ensure that AGVs can move efficiently and safely while completing their tasks.
AGV Navigation Systems
1. Laser Target Navigation
Laser target navigation is one of the most widely used systems in AGVs. It involves a laser scanner that emits beams to detect reflective markers placed along the path. The AGV uses these markers to calculate its position and maintain its course accurately.
2. Inertial (Gyroscopic) Navigation
Inertial navigation systems use gyroscopes to detect changes in direction and make adjustments accordingly. These systems are often paired with transponders embedded in the floor, helping AGVs stay on track and navigate even in areas with limited visual markers.
3. Natural Feature (Natural Targeting) Navigation
This system allows AGVs to use cameras and range-finding sensors to map out and navigate using natural features in their environment, such as walls or landmarks. This method allows AGVs to make more flexible and dynamic route choices, adjusting in real-time to obstacles.
AGV Steering and Control
AGVs are equipped with various steering mechanisms, including differential speed control, steered wheel control, or a combination of both. These systems ensure that the AGV can maneuver precisely and navigate around obstacles while maintaining stability and control.
AGV Traffic Control
To avoid collisions and ensure smooth traffic flow, AGVs employ various traffic control mechanisms such as zone control and collision avoidance systems. These systems help AGVs operate autonomously in environments shared with other robots or human workers, improving safety and efficiency.
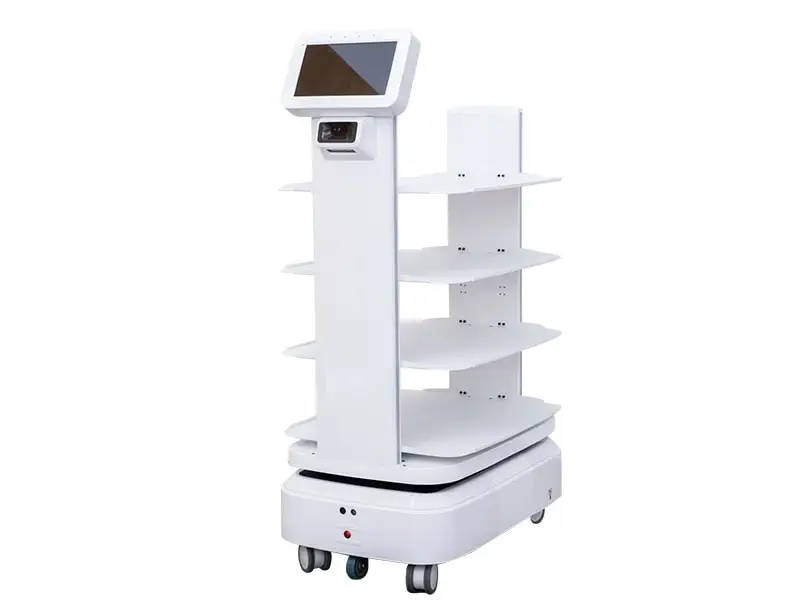
Applications and Industries Using AGVs
AGVs have a broad range of applications across various industries. Below are some key industries where AGVs play a crucial role:
1. Manufacturing Facilities
AGVs are frequently used in manufacturing facilities to move raw materials, work-in-process goods, and finished products. They help streamline the production process by transporting materials to different stages of production, reducing manual labor and improving overall efficiency.
2. Warehouses
In warehouses, AGVs are essential for managing inbound and outbound logistics. They transport goods from receiving docks to storage areas, retrieve items from shelves for order picking, and deliver goods to packaging or shipping zones.
3. Automotive Industry
In automotive manufacturing, AGVs are used to transport materials, assist in assembly line processes, and reduce production delays. By enhancing logistics and material handling, AGVs help automotive manufacturers increase efficiency and reduce congestion.
4. Agriculture
AGVs are also gaining traction in the agricultural industry, where they can automate tasks like planting, harvesting, and crop maintenance. These robots improve precision, reduce labor costs, and help farmers optimize their operations.
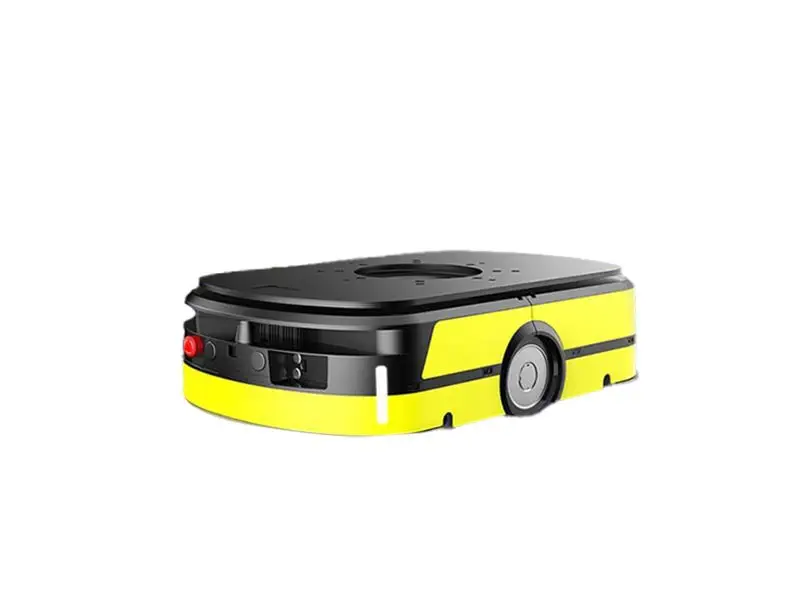
Benefits of Automated Guided Vehicles
AGVs offer numerous benefits that help businesses increase efficiency, reduce costs, and improve safety:
1. Increased Efficiency and Productivity
By automating repetitive tasks, AGVs can significantly enhance operational efficiency. They reduce the need for human labor in material handling, allowing workers to focus on more complex tasks and improving the overall throughput of operations.
2. Consistent Costs
AGVs help businesses manage costs by providing a predictable cost structure. Unlike labor costs, which fluctuate, AGVs require a fixed investment or rental period, offering more stable and manageable expenses over time.
3. Flexibility
AGVs are highly flexible and can easily adapt to changing environments. They can be reprogrammed to follow new routes or perform different tasks, making them suitable for dynamic production or warehouse environments.
4. Improved Safety
AGVs are equipped with sensors and cameras that enable them to detect obstacles and avoid collisions. By reducing human involvement in hazardous tasks, AGVs improve safety in workplaces, lowering the risk of workplace injuries.
5. Predictive Maintenance
AGVs are capable of self-monitoring their performance through sensors, which help predict potential issues before they occur. This feature allows for proactive maintenance, reducing downtime and preventing costly repairs.
Challenges and Limitations of AGVs
Despite their numerous advantages, implementing AGVs can present challenges:
1. Infrastructure Modifications
To integrate AGVs into existing facilities, businesses may need to make changes to the physical environment, such as installing tracks or markers. These modifications can be costly and time-consuming.
2. Choosing the Right AGV
Selecting the appropriate AGV for a specific application involves evaluating factors such as payload capacity, required speed, navigation methods, and compatibility with existing systems. Choosing the wrong AGV can lead to inefficiencies and additional costs.
3. Technology Limitations
AGVs still rely on predefined paths and can encounter difficulties in unpredictable environments. They may require human intervention in complex situations or when encountering obstacles outside of their programmed routes.
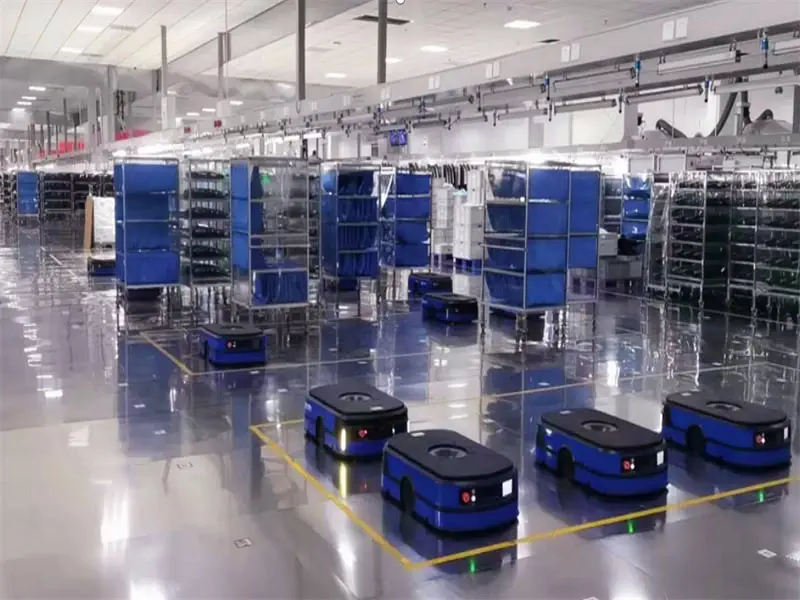
Alternatives to AGVs
While AGVs are an excellent solution for many industrial applications, there are alternatives worth considering:
1. Conveyor Systems
Unlike AGVs, conveyor systems are stationary and require a fixed path. While they are suitable for specific applications, they lack the flexibility and mobility that AGVs offer.
2. Automated Storage and Retrieval Systems (AS/RS)
AS/RS systems provide automated transportation and storage solutions, offering an alternative to AGVs in environments where storage and retrieval tasks are a priority.
3. Autonomous Mobile Robots (AMRs)
AMRs are similar to AGVs but more advanced in their navigation capabilities. AMRs can navigate dynamically, making real-time decisions and adjusting their routes as needed.
Conclusion
Automated Guided Vehicles (AGVs) are transforming industries by providing cost-effective, efficient, and safe solutions for material handling and transportation. From manufacturing to warehousing, AGVs are optimizing processes and increasing productivity. As AGV technology continues to evolve, businesses should consider integrating AGVs into their operations to remain competitive and achieve operational excellence. By evaluating the right AGV solutions and integrating them with existing systems, companies can streamline their logistics and reduce operational costs, setting themselves up for success in a rapidly evolving market.
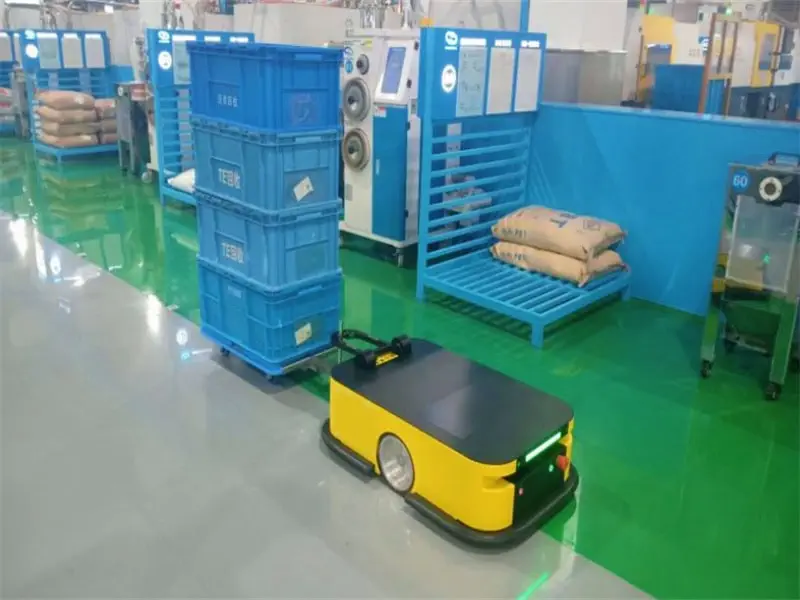