What are Automated Guided Vehicles (AGVs)?
Definition and Explanation of AGVs
Automated Guided Vehicles (AGVs) are self-operating vehicles designed to transport goods within controlled environments such as warehouses, factories, and distribution centers. These vehicles operate autonomously, taking over tasks traditionally done by forklifts, conveyor systems, or manual labor. AGVs are also known as self-guided vehicles or autonomous guided vehicles, and they are integral to modern automation strategies.
Importance of AGVs in Modern Warehousing
In the fast-paced world of modern warehousing, AGVs play a critical role in ensuring the efficient and automated transportation of goods. These systems help to reduce labor costs, improve productivity, and increase the accuracy of operations. By automating material handling tasks, AGVs enhance the overall effectiveness of supply chains and contribute to a safer and more streamlined work environment.
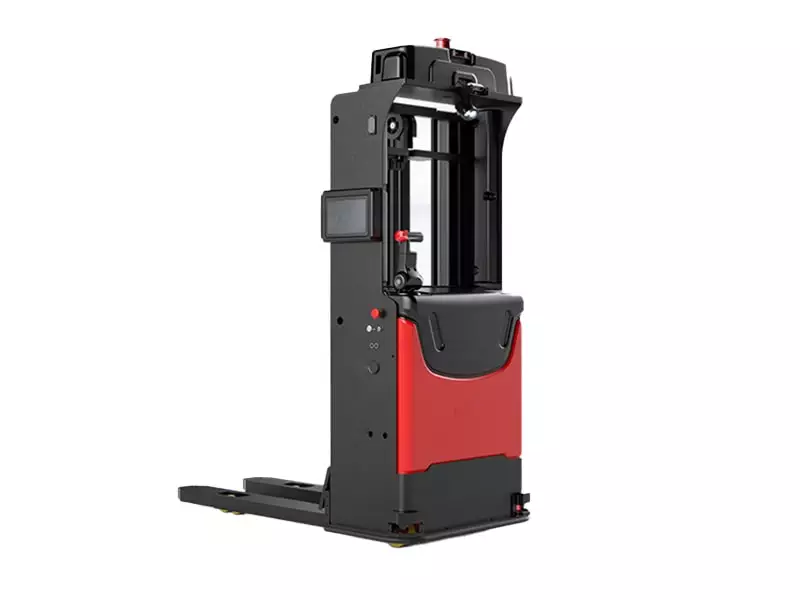
Types of Automated Guided Vehicles
- Automated Guided Carts (AGCs)
AGCs are the simplest form of AGVs. These vehicles typically follow predefined paths, such as magnetic tracks or guide wires. They are ideal for transporting smaller loads or materials within a facility, offering a cost-effective solution for businesses with less complex automation needs.
- Forklift AGVs
Forklift AGVs are designed to mimic the functions of conventional forklift trucks but operate autonomously. They are equipped with forks to lift and place loads at various heights, making them suitable for handling pallets and other unitized loads. These vehicles can carry heavier loads and perform a variety of tasks without the need for a human operator.
- Unit Load AGVs
Unit Load AGVs are designed to transport individual unit loads like pallets, containers, or racks. These AGVs often come with platforms or forks to support and move the loads efficiently. Unit Load AGVs are widely used in facilities that require the transport of large quantities of goods or raw materials.
- Towing AGVs (Tuggers)
Towing AGVs, or tuggers, are used to pull or tow carts, trailers, or other wheeled devices autonomously. They are equipped with a hitch or coupling mechanism to connect and transport multiple loads at once. Tuggers are particularly useful in large warehouses and manufacturing environments where goods need to be transported across long distances.
- Autonomous Mobile Robots (AMRs)
Autonomous Mobile Robots (AMRs) are an advanced form of AGVs, equipped with sensors and cameras that allow them to understand and interact with their surroundings in real time. AMRs are highly versatile and can navigate complex, dynamic environments without the need for predefined paths.
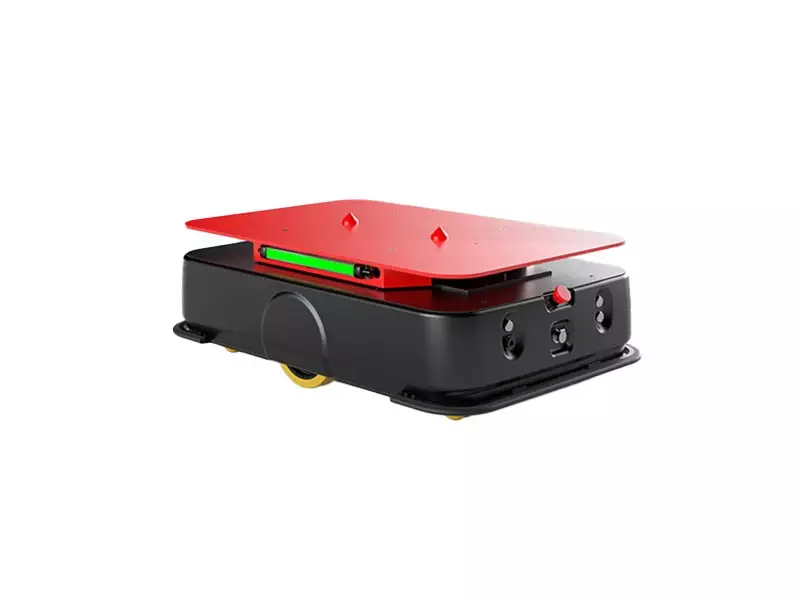
How AGVs Work
Navigation Systems
AGVs use several navigation systems to operate efficiently within their environment. These systems include laser target navigation, magnetic tape, and natural feature navigation. These technologies enable AGVs to follow predefined paths while avoiding obstacles and ensuring they stay on course.
Steering and Control
AGVs use various steering mechanisms to control their movement. Differential speed control and steered wheel control are common methods, allowing AGVs to change direction or adjust speed. Many AGVs also use zone control sensors to prevent collisions, ensuring smooth and safe operation.
Traffic Control and Management
In environments with multiple AGVs, traffic control systems are used to manage their movements. These systems ensure that AGVs coordinate their operations and avoid collisions with other vehicles, obstacles, or workers. Advanced management systems can adjust the AGVs’ routes in real time to optimize workflow and prevent bottlenecks.
Applications of AGVs in Warehousing
- Transportation of Raw Materials
AGVs are often used to transport raw materials from receiving areas to storage or directly to production lines. This ensures that materials are delivered on time and without human error, reducing delays in production processes.
- Work-in-Process (WIP) Applications
In manufacturing environments, AGVs move parts or materials between workstations, streamlining the flow of goods and reducing the need for manual labor. This improves the overall efficiency of production lines and minimizes downtime.
- Handling Finished Goods
Once production is complete, AGVs are used to transport finished goods to storage or shipping areas. By automating this process, businesses can speed up order fulfillment and reduce the risk of damage to products.
- Inbound and Outbound Handling
AGVs are also critical in inbound and outbound logistics operations. They can assist in stock replenishment, picking processes, and transportation of goods to the appropriate shipping or receiving areas.

Benefits of AGVs in Warehousing
- Increase Efficiency and Productivity
By automating material handling tasks, AGVs eliminate the need for manual labor in repetitive jobs, allowing workers to focus on higher-value tasks. This improves overall warehouse efficiency and increases throughput.
- Consistent Costs and Reduced Labor Expenses
AGVs can be acquired on a per-unit or per-rental basis, allowing businesses to better control costs. Since they reduce the need for manual labor, companies can significantly cut down on labor-related expenses.
- Flexibility and Adaptability in Warehouse Operations
AGVs are highly flexible and can easily adapt to changing warehouse layouts. Some models even offer the ability to re-route in response to obstacles or operational demands, making them an excellent solution for dynamic environments.
Industries Using AGVs
- Manufacturing Facilities
In manufacturing, AGVs are used to transport raw materials, work-in-process goods, and finished products. They streamline material handling processes, improve efficiency, and reduce downtime in production lines.
- Warehouse and Distribution Centers
AGVs play a pivotal role in warehouse and distribution centers by automating the picking, sorting, and shipping of goods. This increases throughput and helps ensure that products are delivered on time.
- E-Commerce and Retail Fulfillment Centers
E-commerce businesses rely on AGVs to enhance order fulfillment and improve shipping efficiency. By automating the handling and transportation of products, AGVs help speed up the order-to-shipment process.
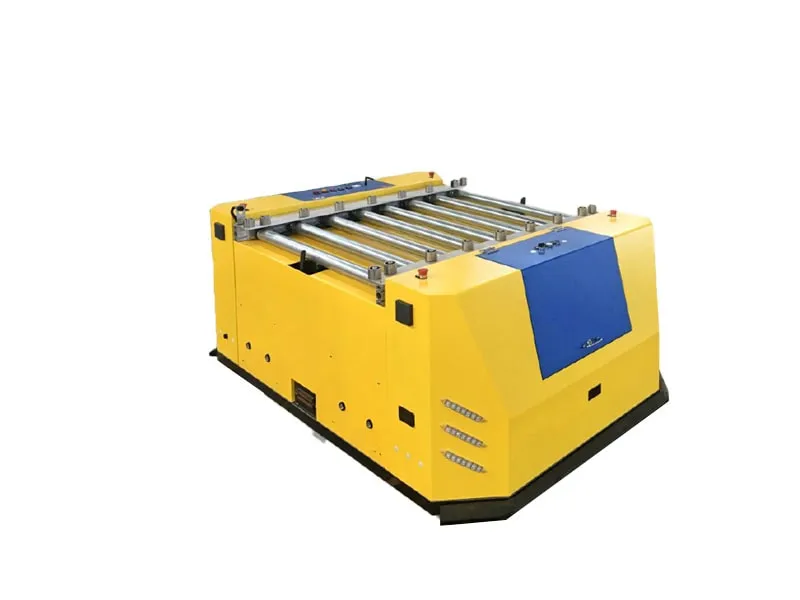
Implementing AGVs in Warehouse Operations
- Assessing Warehouse Operations and Needs
Before implementing AGVs, it is crucial to assess the specific needs and layout of the warehouse. This includes evaluating factors such as inventory management, workflow, and potential obstacles to AGV operation.
- Selecting the Right AGV Type and Navigation System
Choosing the right type of AGV and navigation system is essential for successful implementation. This decision should be based on factors like load capacity, speed, and the complexity of the warehouse environment.
- Training and Support for AGV Operators and Maintenance Personnel
Proper training for AGV operators and maintenance personnel is crucial to ensure that these vehicles are used effectively and safely. Ongoing support and troubleshooting services will also be necessary to keep the systems running smoothly.
Conclusion
Automated Guided Vehicles (AGVs) are an essential part of modern warehouse automation, helping businesses improve efficiency, reduce costs, and enhance safety. With their ability to transport goods autonomously and adapt to changing environments, AGVs are transforming supply chains and warehouse operations.
As industries continue to seek more automated solutions, integrating AGVs into operations is becoming increasingly vital for staying competitive.
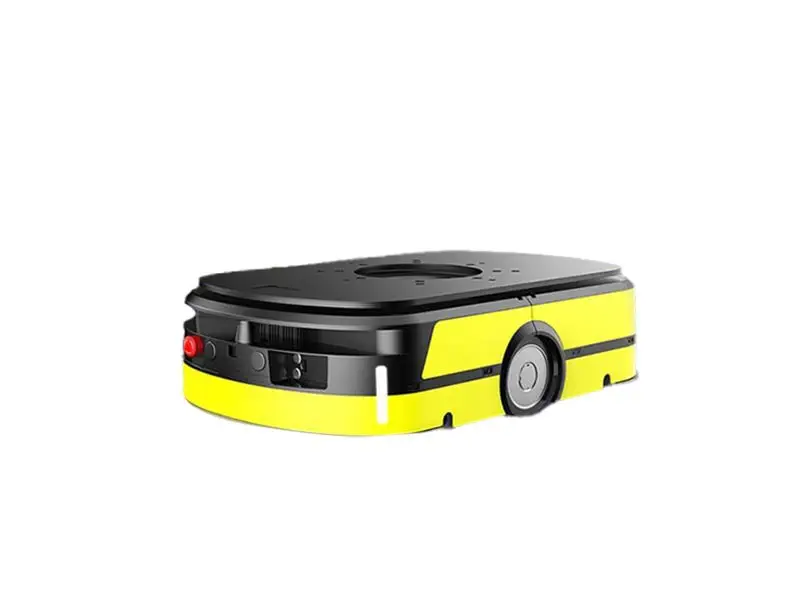