Introduction to AGVs
Automated Guided Vehicles (AGVs) are revolutionizing industries by automating the transport of materials within controlled environments. These self-driving vehicles navigate without human operators, making them a game-changer in various sectors, including manufacturing, logistics, and warehousing. AGVs not only enhance operational efficiency but also contribute significantly to safety and productivity improvements. In this article, we’ll dive into AGV fundamentals, types, navigation systems, benefits, and their diverse applications.
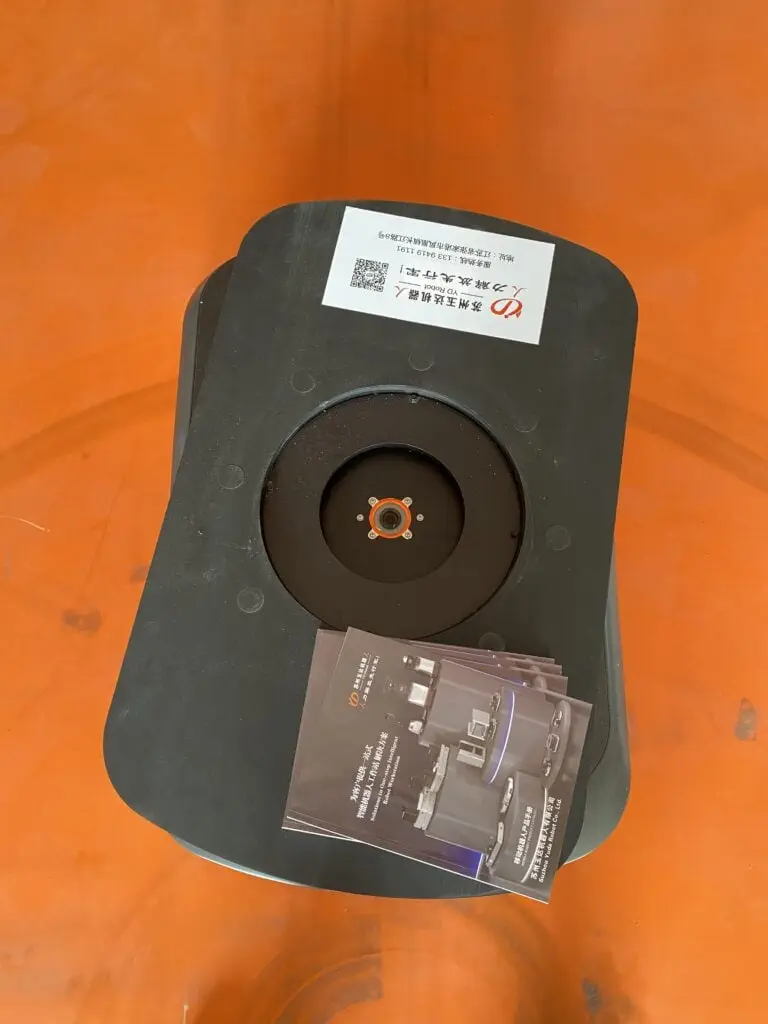
What is an Automated Guided Vehicle (AGV)?
An Automated Guided Vehicle (AGV) is a mobile robot that autonomously transports materials or goods within a predefined environment. Unlike traditional vehicles, AGVs operate without a human driver. They are widely used in large facilities like factories and warehouses to transport heavy loads efficiently and reliably. AGVs are essential components of automated production lines, helping businesses achieve higher operational speeds while reducing labor costs.
Brief History of AGVs
The concept of AGVs dates back to the mid-20th century, where they were initially employed to speed up material handling in warehouses and production centers. Early AGVs relied on wire-based navigation systems, but as technology evolved, so did AGVs. Modern AGVs now use advanced navigation technologies like laser guidance, machine vision, and sensors to navigate complex environments autonomously.
The Importance of AGVs in Modern Production Lines
In today’s fast-paced industrial world, AGVs play a pivotal role in increasing production efficiency. By automating the transport of goods and materials, AGVs minimize human intervention, reduce errors, and optimize workflows. They also improve safety by removing the risks associated with human-operated machinery and by reducing workplace accidents. AGVs contribute to a streamlined supply chain by operating continuously, enabling round-the-clock productivity.
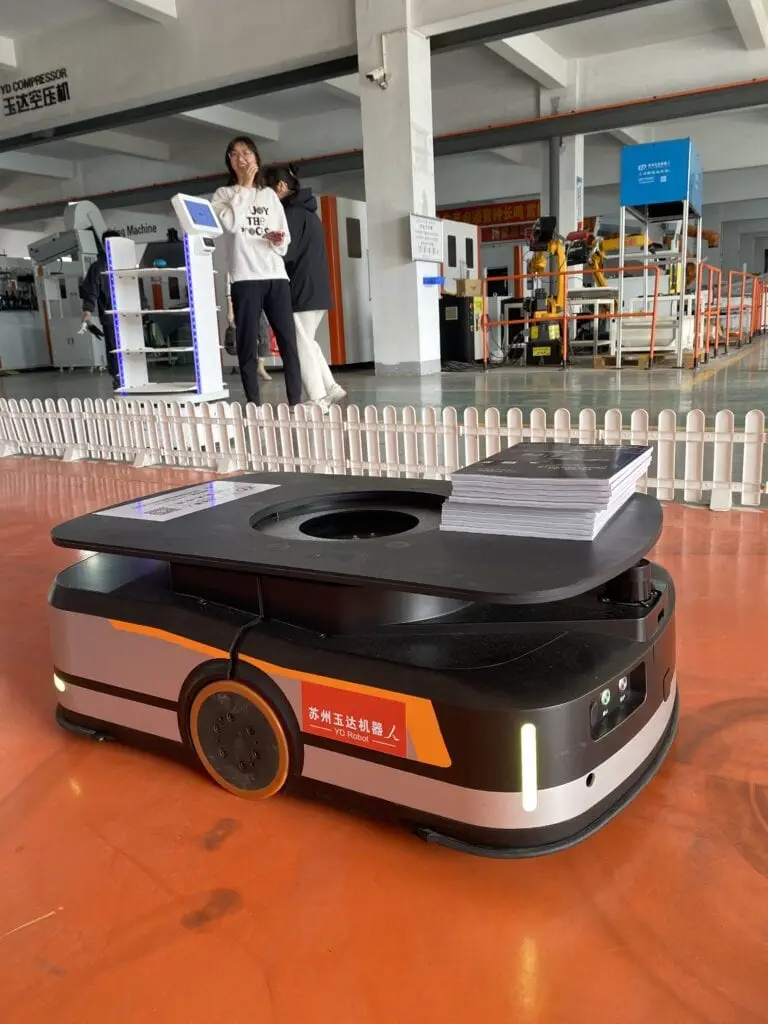
Types of Automated Guided Vehicles (AGVs)
AGVs come in various configurations to meet the needs of different industries. The most common types include:
- Automated Guided Carts (AGCs)
- These are simple AGVs that typically follow predefined paths, such as magnetic tracks or wire-guided routes. AGCs are suitable for moving smaller loads and are commonly used in manufacturing and warehousing.
- Forklift AGVs
- Designed to mimic traditional forklifts, these AGVs can lift and transport materials at various heights without the need for a human operator. Forklift AGVs are commonly used in large-scale warehouses and manufacturing facilities.
- Unit Load AGVs
- These vehicles are designed to carry unit loads, such as pallets or containers. With platforms or forks, unit load AGVs can transport substantial goods from one point to another in industries like logistics and warehousing.
- Towing AGVs (Tuggers)
- Towing AGVs are used to pull carts, trailers, or other wheeled devices autonomously. These AGVs are designed to tow materials across long distances, making them ideal for transporting bulk goods.
- Heavy Burden Carriers
- Built to handle heavy-duty loads, these AGVs are equipped with advanced steering options and often feature self-loading capabilities. Heavy burden carriers are commonly used in manufacturing and logistics environments that require robust material handling.
- Hybrid AGVs
- Hybrid AGVs offer both autonomous and manual operation. These versatile vehicles can switch between automatic navigation and manual control, providing flexibility for operations that need a human touch in certain scenarios.
- Autonomous Mobile Robots (AMRs)
- Though similar to AGVs, AMRs use advanced sensors, onboard AI, and maps to navigate dynamically. AMRs can alter their path in real-time to avoid obstacles or adjust to changes in the environment, making them a highly flexible option for diverse industries.
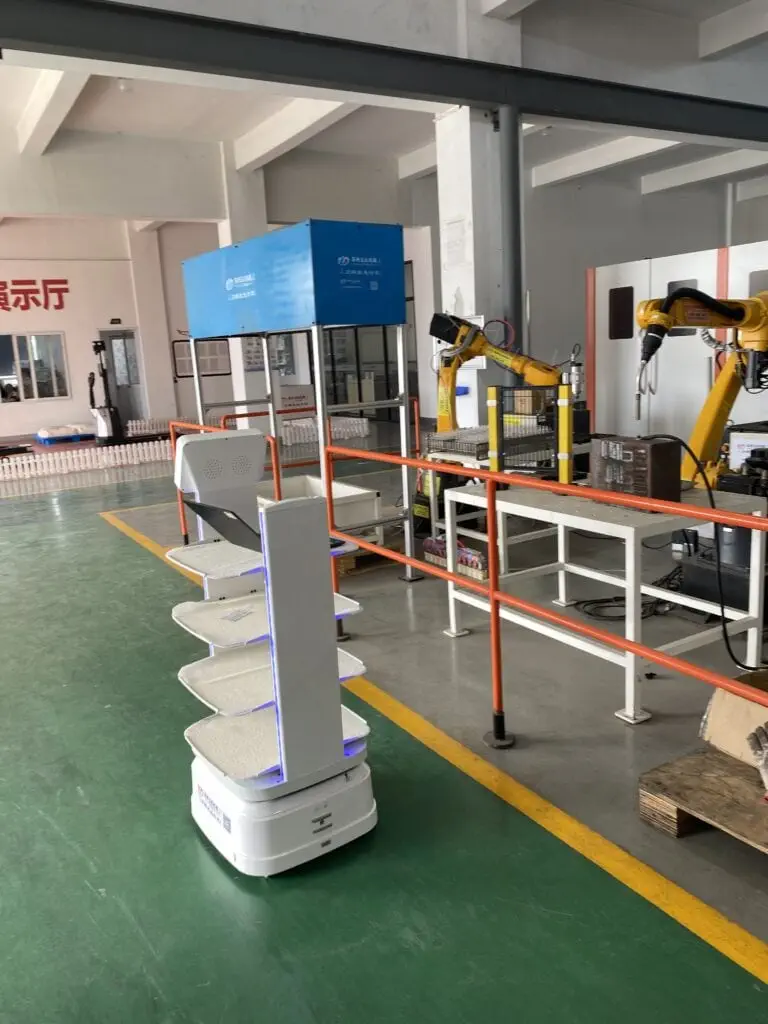
AGV Navigation and Control Systems
AGVs rely on sophisticated navigation and control systems to ensure precise and safe movement. Some of the common navigation technologies include:
- Laser Target Navigation
- This method uses retro-reflective laser guidance to determine the AGV’s position within its environment. Laser target navigation is accurate and commonly used in many modern AGVs.
- Inertial (Gyroscopic) Navigation
- Inertial navigation systems use transponders embedded in the floor to help AGVs track their movements. A gyroscope detects any deviation from the path and corrects the vehicle’s course, ensuring it stays on track.
- Natural Feature Navigation
- Utilizing cameras and sensors, natural feature navigation allows AGVs to identify and follow unique features within their environment. This technology is particularly useful in complex or changing environments.
How AGVs Work
AGVs operate using a combination of sensors, software, and mechanical components. Their movement is controlled through differential speed, steering wheel control, or a combination of both. AGVs are capable of moving in various directions, including forward, backward, left, right, and even diagonally, enabling them to navigate tight spaces. In addition, AGVs can rotate in place for precise handling of materials.
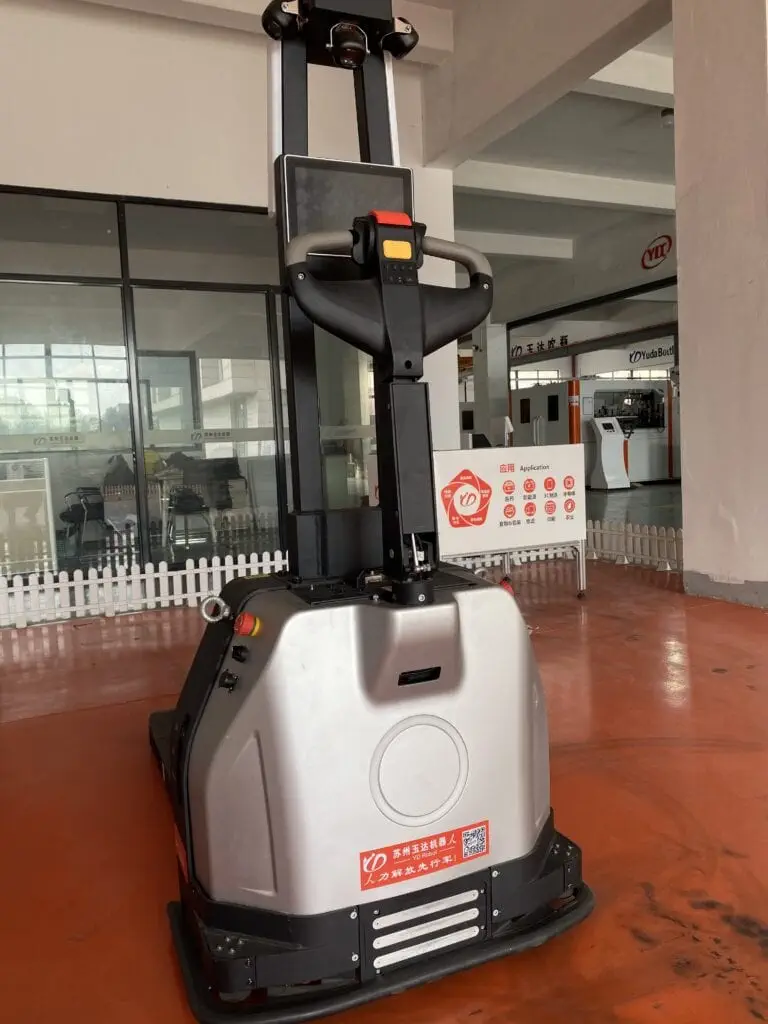
Benefits of AGV Systems
- Increased Efficiency and Productivity
- AGVs operate continuously and autonomously, allowing for round-the-clock material handling without human intervention. This leads to higher throughput and less downtime.
- Consistent Cost Management
- By reducing labor costs and minimizing the risk of accidents, AGVs provide predictable and consistent operational expenses.
- Improved Flexibility
- AGVs can be adapted for different tasks and industries, offering customizable solutions for businesses with unique material handling needs.
- Space Efficiency
- AGVs require less space compared to traditional automation systems, such as conveyor belts, and can operate in tight spaces like narrow aisles.
- Enhanced Safety
- AGVs reduce the need for human labor in dangerous environments, thus improving workplace safety. Their ability to detect and avoid obstacles helps minimize the risk of accidents.
Applications of Automated Guided Vehicles
- Handling Raw Materials
- AGVs are used to move raw materials to production lines or storage areas. This automation streamlines material handling and improves the overall efficiency of manufacturing processes.
- Work-in-Process Movement
- AGVs transport materials or components between production stages, optimizing the flow of materials through the manufacturing process.
- Finished Product Handling
- After production, AGVs can transport finished products to storage or shipping areas, reducing the risk of product damage from manual handling.
- Inbound and Outbound Handling
- AGVs automate stock replenishment, picking, and shipping, streamlining warehouse operations and reducing human labor.
- Automated Storage and Retrieval
- AGVs can be integrated with Automated Storage and Retrieval Systems (AS/RS) to transport items to and from storage areas efficiently.
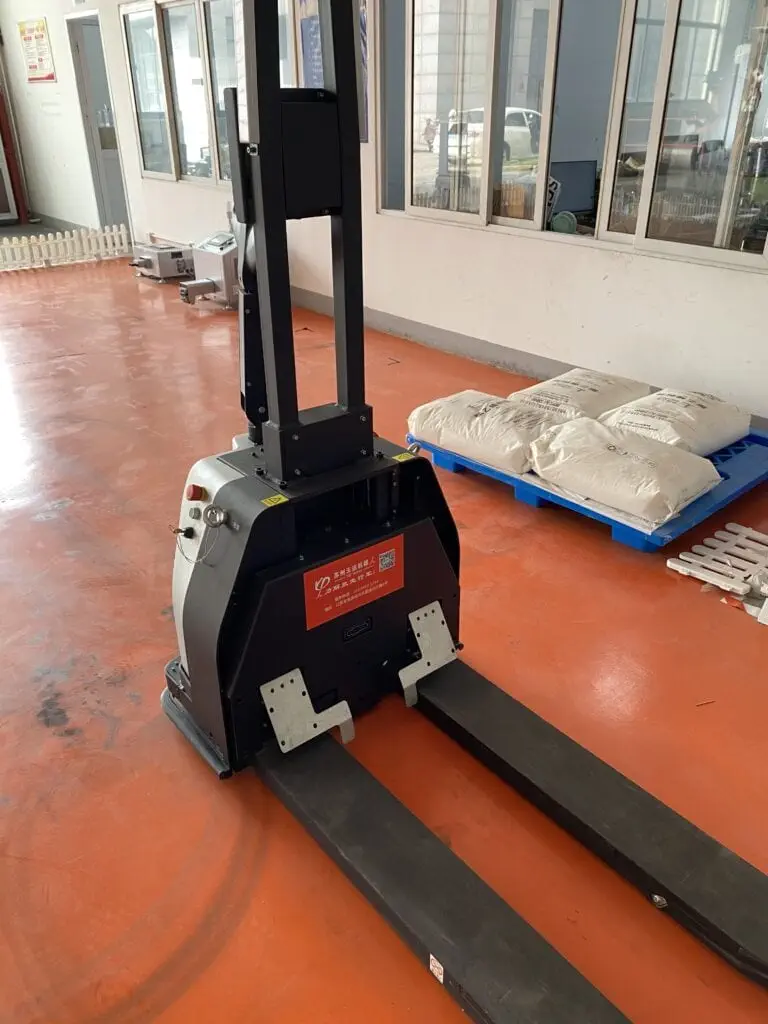
Industries That Benefit from AGVs
- Warehousing and Logistics
- AGVs are extensively used in warehouses and distribution centers to automate material transport, improving efficiency and reducing labor costs.
- Manufacturing
- From raw material transport to finished product handling, AGVs are integral to streamlining manufacturing operations.
- Healthcare
- AGVs are increasingly being used in hospitals to transport medications, clean linen, and waste, reducing the need for human involvement in these tasks.
- Retail and E-commerce
- AGVs help with order picking, packing, and sorting, enabling e-commerce businesses to fulfill orders quickly and accurately.
Implementing an AGV System
- Planning and Design
- Designing a custom AGV system is essential to meet specific operational needs. Proper planning ensures that the system integrates seamlessly with existing infrastructure and improves overall productivity.
- Installation and Testing
- Installing an AGV system requires careful setup and testing to ensure proper function and integration with other systems.
Conclusion: The Future of AGVs
AGVs are increasingly becoming a cornerstone of modern industrial automation, offering businesses the flexibility to optimize material handling, improve efficiency, and reduce costs. As technology advances, AGVs will continue to evolve, offering even greater capabilities and further improving operations across industries. Investing in AGV systems can provide substantial long-term benefits, positioning businesses for greater success in an increasingly automated world.
Explore AGV solutions to enhance your warehouse or manufacturing processes today!
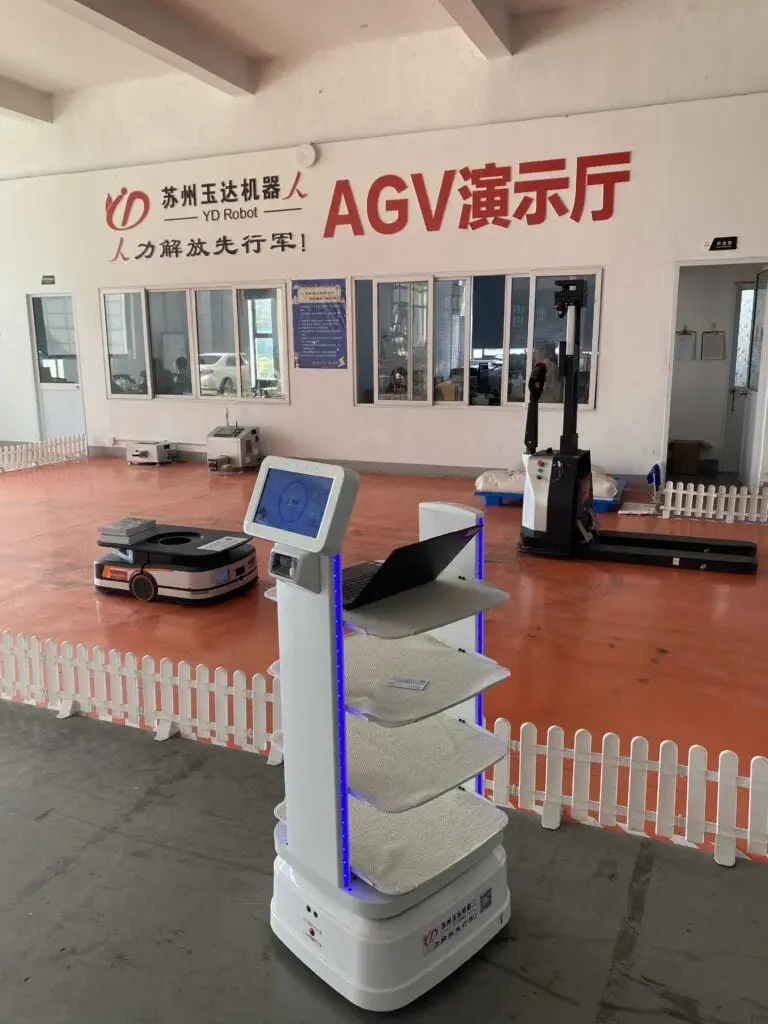