What is Plastic Extrusion? Plastic extrusion is a high-volume manufacturing process that involves the homogenous melting of a thermoplastic material. Dating back to the early 19th century, with the first thermoplastic extrusion occurring in 1935, this process has become indispensable in modern manufacturing. It is widely used in various industries, including construction, packaging, electrical, automotive, and consumer goods, highlighting the significance of “plastic extrusion line” in today’s industrial landscape.
Key Factors to Consider When Setting Up an Extrusion Line for Plastic Processing
Material Type: The choice of plastic material, such as PVC, HDPE, or PP, greatly influences the selection of extrusion equipment and process parameters. Different materials have varying melting points, viscosities, and flow characteristics, which must be considered to optimize the “extrusion plastic process” and achieve the desired product properties.
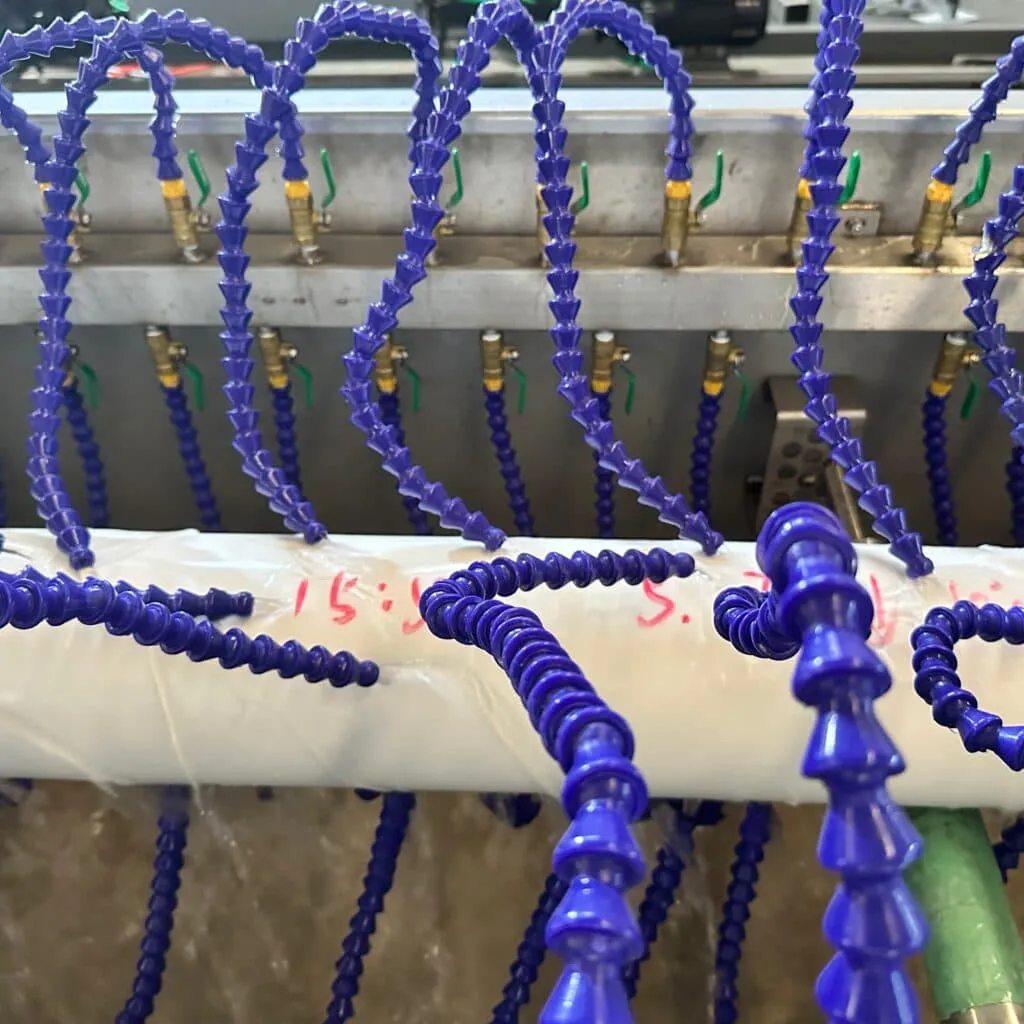
Extruder Type: When it comes to extruders, there are single screw extruders and twin screw extruders. Single screw extruders are favored for their low cost, simple design, durability, and reliability. They offer a favorable performance-to-cost ratio, making them a popular choice for many applications. On the other hand, twin screw extruders provide enhanced stability, superior performance in exhausting air and volatile fumes, increased production speed, and improved mixing capabilities. The choice between the two depends on specific production needs and the desired outcomes of the “extruder plastic” process.
Die Design: The die is a critical component in the extrusion line, as it determines the shape and dimensions of the final product. A well-designed die ensures uniform flow of the molten plastic, resulting in consistent product dimensions and high-quality output. It is essential to work with experienced die designers to create a die that meets the specific requirements of the product being manufactured.
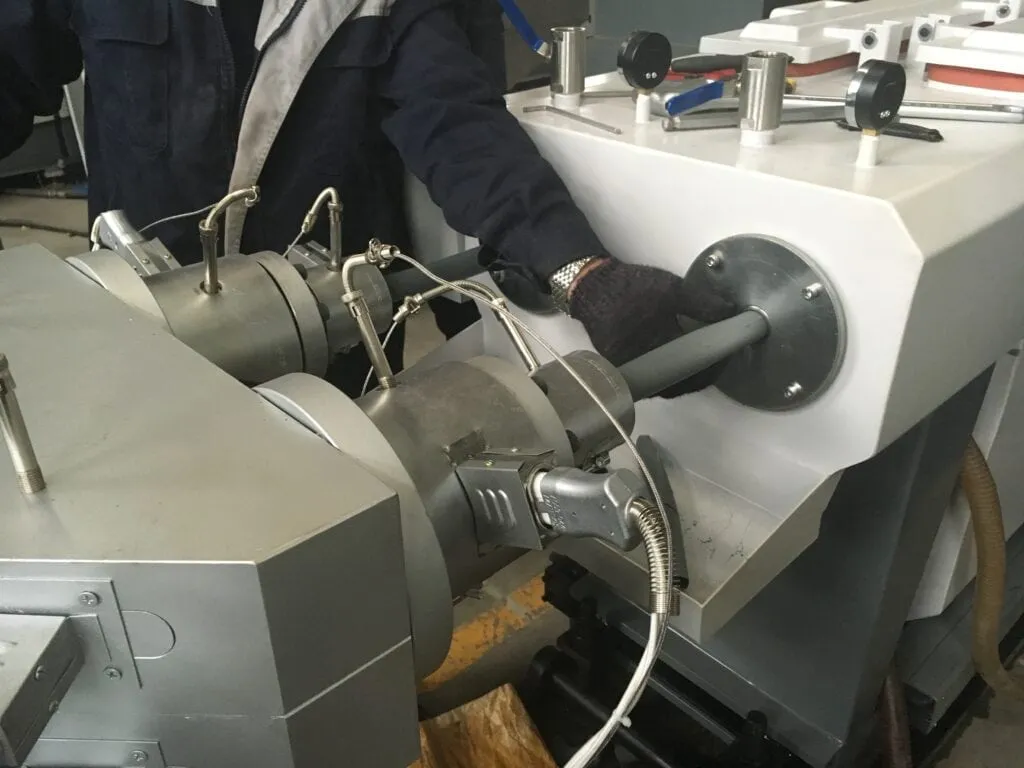
Temperature and Pressure Control: Precise temperature and pressure management are vital in the “extrusion plastic process.” The temperature affects the melting and flow of the plastic material, while pressure influences the density and quality of the extruded product. Advanced control systems are used to monitor and regulate these parameters, ensuring optimal conditions for producing high-quality products and maintaining production efficiency.
Production Speed and Efficiency: Balancing production speed with product quality is a key consideration in setting up an extrusion line. Different extrusion lines have varying capabilities in terms of throughput and speed. It is important to select an extrusion line that can meet the production demands without compromising on product quality. Modern extrusion lines often incorporate features such as high-speed screw drives and efficient cooling systems to enhance production efficiency while maintaining product integrity.
Automation and Control Systems: Modern plastic extrusion lines come equipped with advanced automation and control systems. These systems offer numerous benefits, such as improved process control, increased production efficiency, reduced operator error, and enhanced product quality. They enable real-time monitoring of various process parameters, allowing for quick adjustments and optimization of the extrusion process. Investing in an extrusion line with robust automation and control capabilities can provide a significant competitive advantage in the plastic processing industry.
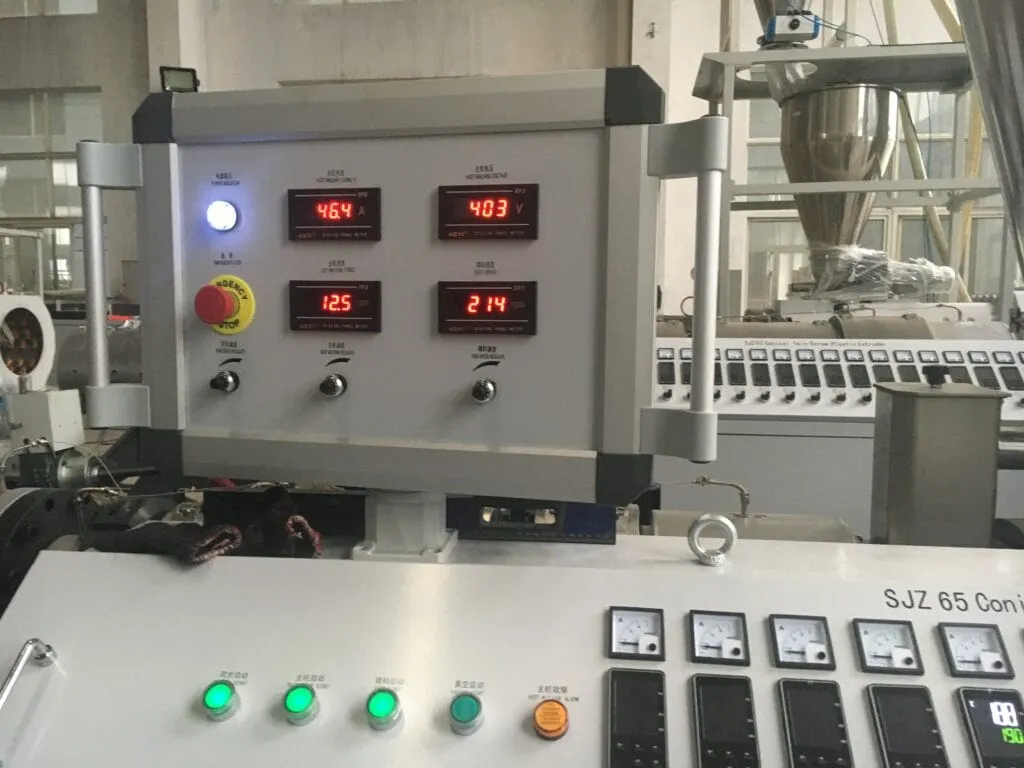
The Plastic Extrusion Process
Step one: Adding additives – This step involves adding colorants, UV inhibitors, and other chemicals to the plastic material to enhance its properties. These additives play a crucial role in improving the performance and appearance of the final product, making them an essential part of the “extrusion plastic process.”
Step two: Moltening material – The plastic material is fed into the hopper and then conveyed into the barrel of the extruder. Here, it is subjected to heat and pressure, causing it to melt and form a homogeneous molten mass. The extruder’s screw design and speed are carefully controlled to ensure proper melting and mixing of the material.
Step three: Forming the mold – Once the plastic material is molten, it is pushed through the die, which gives it the desired shape and profile. The die design is critical in this step, as it determines the final dimensions and appearance of the extruded product. The molten plastic is forced through the die under high pressure, ensuring a consistent and accurate shape.
Step four: Cooling – After the plastic product is formed, it needs to be cooled to solidify it. Cooling systems, such as water baths or air cooling units, are used to rapidly cool the extruded product. Proper cooling is essential to prevent product deformation and ensure dimensional accuracy.
Types of Plastic Extruders
Single-screw extruder: As the most prevalent continuous extruder, the single-screw extruder is favored for its low cost, simple design, durability, reliability, and favorable performance-to-cost ratio. It is suitable for a wide range of applications and is often the first choice for many manufacturers looking to invest in “plastic extrusion line” equipment.
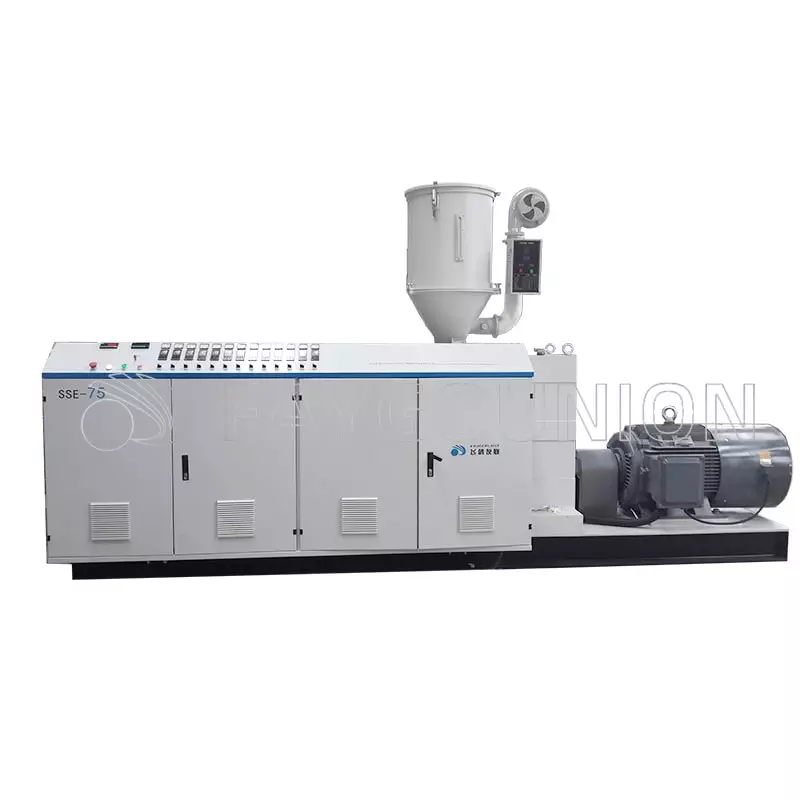
Twin Screw Extruders: Offering enhanced stability, superior performance in exhausting air and volatile fumes, increased production speed, and improved mixing capabilities, twin screw extruders are ideal for more demanding applications. They are particularly useful when working with materials that require thorough mixing or when high production volumes are needed.
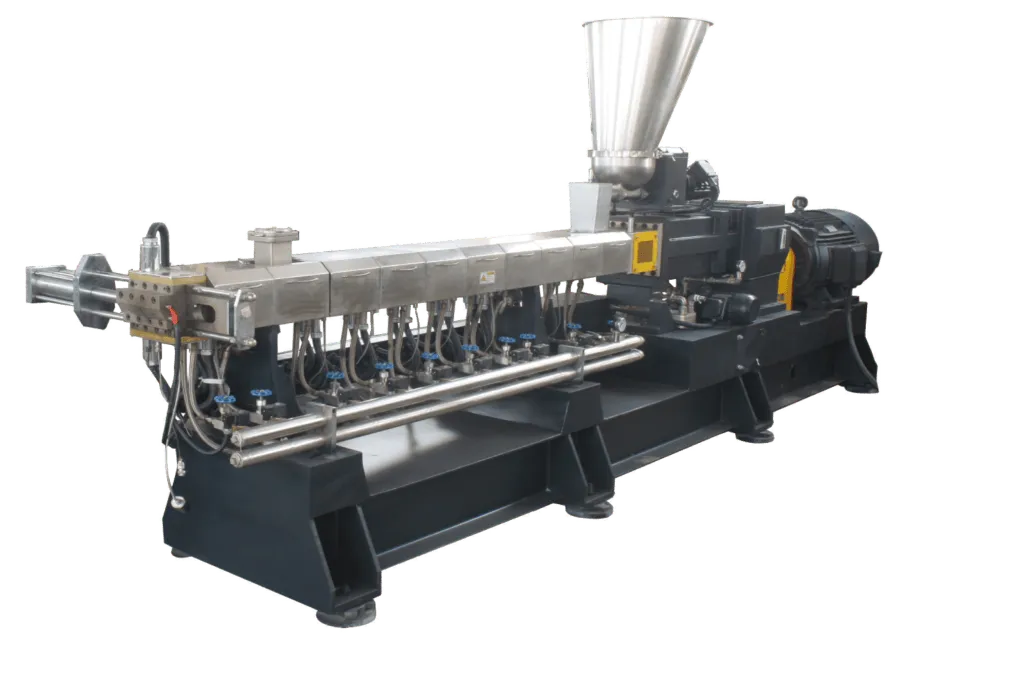
Multiscrew extruder with more than two screws: Featuring multiple interlocking screws, multiscrew extruders are used for specific applications that require advanced mixing and processing capabilities. They provide even greater control over the extrusion process, allowing for the production of complex and high-quality products.
Plastic Material of Plastic Extrusion line
Common plastic materials used in extrusion include polyethylene (PE), polypropylene, polyacetal, acrylic, nylon, polystyrene, polyvinyl chloride (PVC), and acrylonitrile butadiene styrene (ABS). Each material has its unique properties, such as flexibility, durability, and resistance to corrosion, making them suitable for different applications. Factors affecting material selection include properties, cost, and availability. The choice of material will depend on the specific requirements of the product being manufactured and the desired performance characteristics.
Benefits of Plastic Extrusion
High production rates: One of the significant advantages of plastic extrusion is its ability to produce large quantities of products in a relatively short amount of time. This makes it an ideal manufacturing process for mass production, allowing businesses to meet high demand efficiently.
Low production costs: Compared to other manufacturing processes, plastic extrusion is cost-effective. The relatively simple design of the extrusion equipment, combined with the ability to produce large volumes, results in lower production costs per unit. This cost advantage can provide a competitive edge in the market, especially for businesses looking to produce cost-sensitive products.
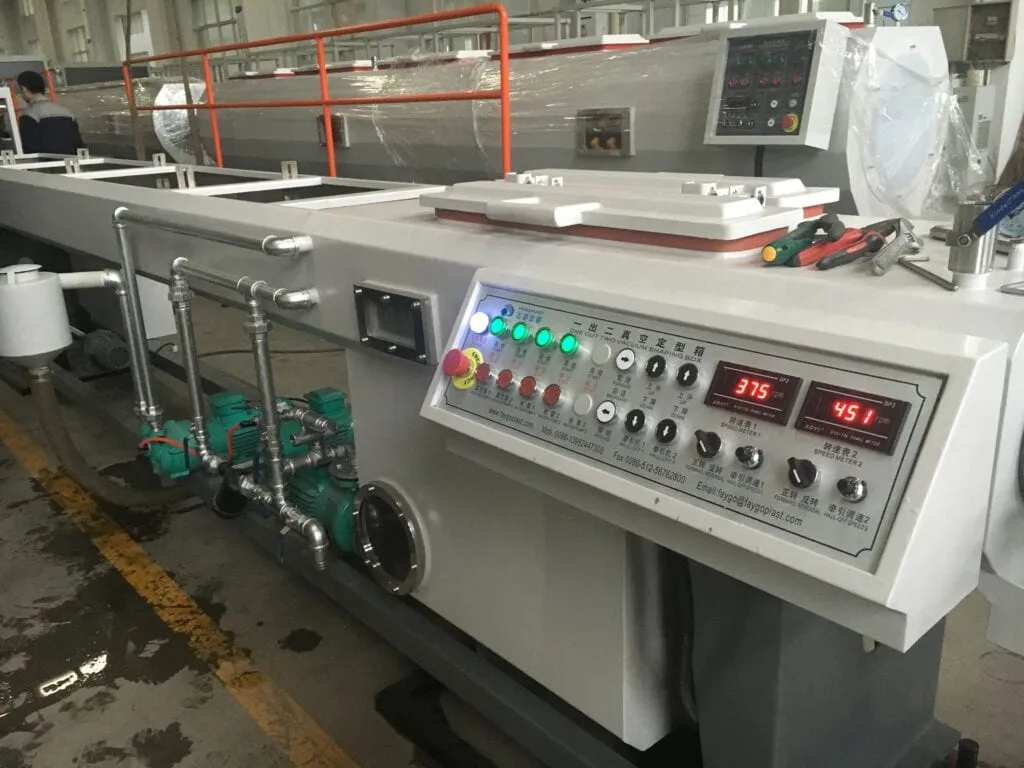
Flexibility in design and material selection: Plastic extrusion offers a high degree of flexibility in terms of design and material selection. Manufacturers can easily customize the shape, size, and profile of the extruded products to meet specific customer requirements. Additionally, the wide range of available plastic materials allows for the production of products with varying properties, such as flexibility, strength, and resistance to chemicals. This flexibility makes plastic extrusion a versatile manufacturing process suitable for a diverse range of applications.
Common Challenges in Plastic Extrusion
Material Contamination: Improper handling of materials can lead to product defects in the “extrusion plastic process.” Contaminants such as dirt, moisture, or foreign particles can mix with the plastic material, affecting its properties and causing defects in the final product. It is crucial to implement strict quality control measures and proper material handling procedures to prevent material contamination and ensure the production of high-quality products.
Machine Maintenance: Regular maintenance of the extrusion equipment is essential to avoid downtime and reduce wear on components. Failure to maintain the machinery can result in decreased production efficiency, increased production costs, and compromised product quality. Manufacturers should establish a comprehensive maintenance schedule and invest in the necessary resources to keep the equipment in optimal working condition.
Product Quality: Maintaining consistent product quality, especially with materials that are sensitive to temperature and pressure, can be a challenge in plastic extrusion. Factors such as variations in material properties, fluctuations in process parameters, and die wear can affect the quality of the extruded products. Implementing robust quality control systems, monitoring process parameters in real-time, and conducting regular inspections can help identify and address quality issues promptly, ensuring the production of high-quality products.
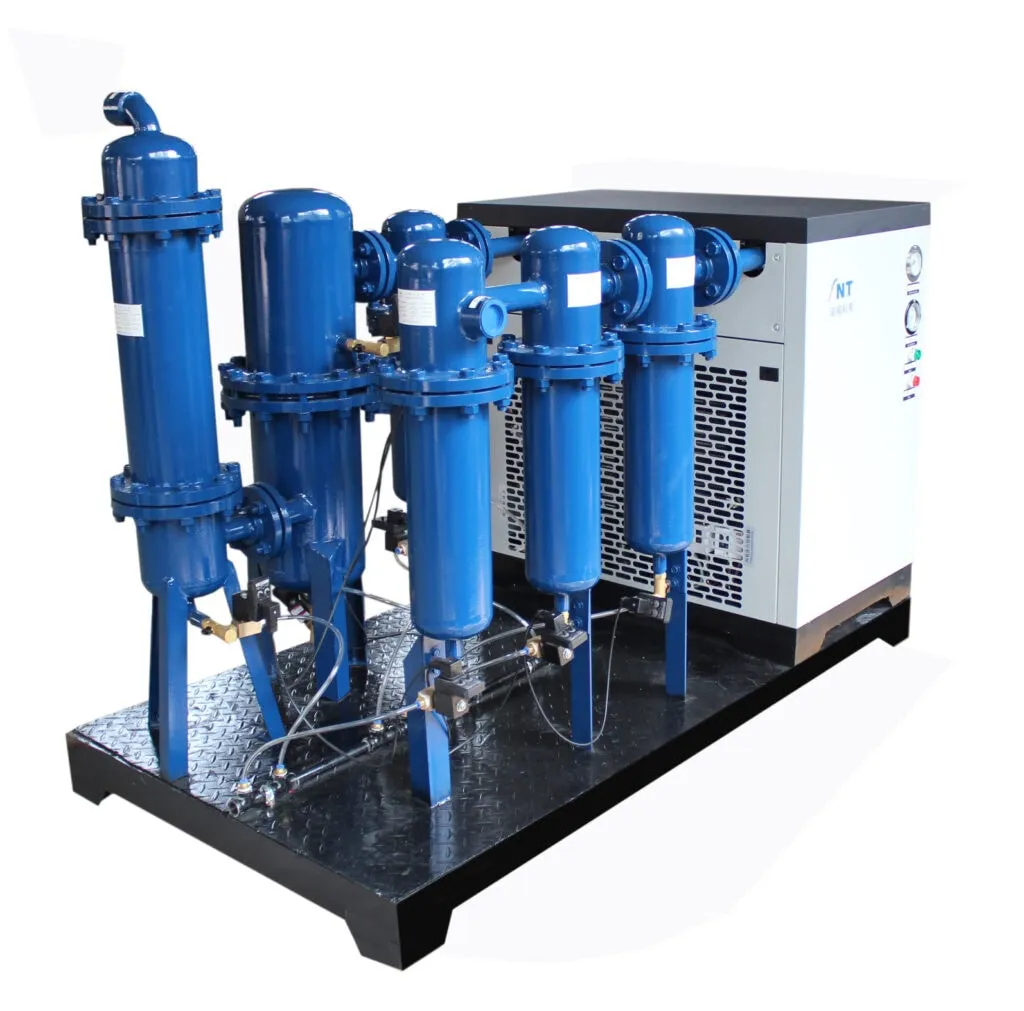
Optimizing Your Plastic Extrusion Line
Choosing the Right Extruder: To choose the best plastic extruder for your production requirements, it is important to consider factors such as production volume, material type, product complexity, and budget. Consulting with experienced suppliers and industry experts can provide valuable insights and guidance in selecting the most suitable extruder for your specific needs.
Upgrading Technology: Upgrading to more energy-efficient or faster machines can offer significant benefits in terms of production efficiency and cost savings. Modern extrusion equipment often incorporates advanced technologies such as improved screw designs, better temperature control systems, and enhanced automation features. Investing in upgraded technology can help businesses stay competitive in the market and meet increasing production demands.
Training and Expertise: Having skilled operators who understand how to fine-tune the extrusion process for optimal results is crucial. Proper training and continuous skill development of the workforce can lead to improved product quality, increased production efficiency, and reduced downtime. Manufacturers should invest in training programs and provide opportunities for their employees to stay updated with the latest advancements in plastic extrusion technology.
Quality Assurance: Implementing best practices for quality control during the extrusion process is essential to ensure the production of high-quality products. This includes regular inspections of raw materials, in-process quality checks, and final product testing. Establishing a comprehensive quality management system can help identify and address quality issues at an early stage, reducing the risk of defects and rework.
Applications of Plastic Extrusion
Wire insulation: Plastic extrusion is widely used to create insulation for wires and cables. The process allows for the production of thin, uniform layers of insulation that provide excellent electrical insulation properties, protecting the conductive wires from damage and ensuring the safe and efficient transmission of electricity.
Pipes and tubes: The manufacturing of pipes and tubes for various industries, such as plumbing, construction, and automotive, relies heavily on plastic extrusion. The process enables the production of pipes and tubes with precise dimensions, consistent wall thickness, and excellent mechanical properties. These products are lightweight, durable, and resistant to corrosion, making them ideal for a wide range of applications.
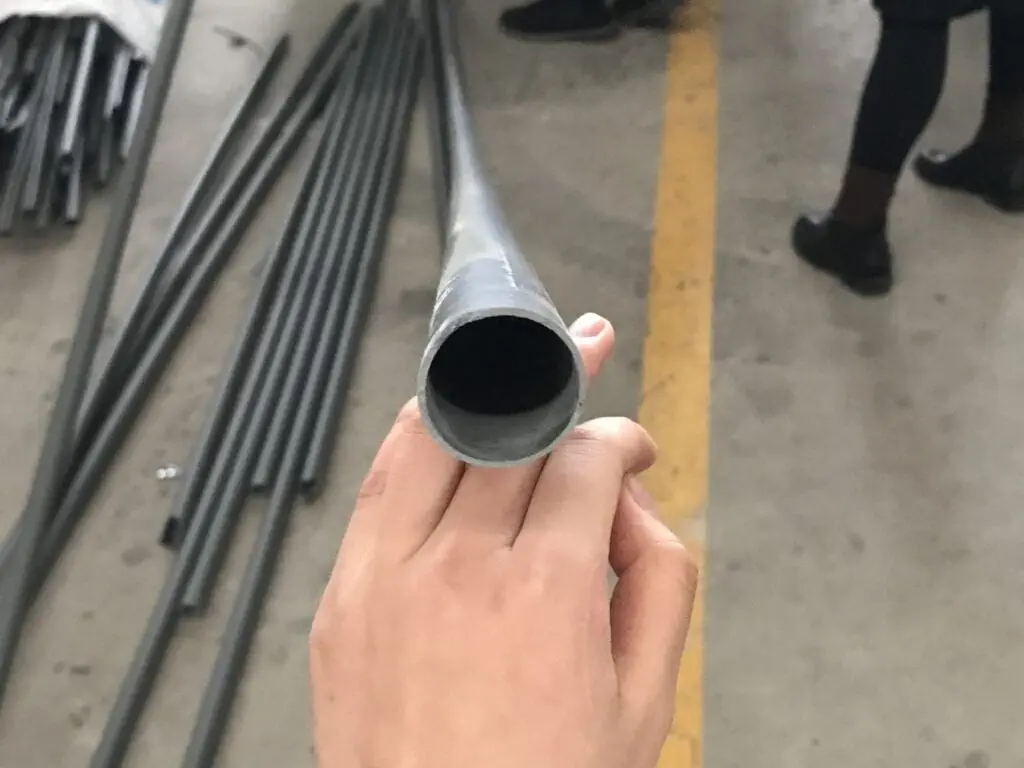
Windows and doors: Plastic extrusion is used to create window and door frames, offering several advantages over traditional materials. The extruded plastic profiles are lightweight, easy to install, and provide good insulation properties. They are also resistant to weathering, fading, and warping, ensuring long-lasting performance and low maintenance requirements.
Blinds and shades: The production of blinds and shades also benefits from plastic extrusion. The process allows for the creation of thin, flexible plastic slats that can be easily adjusted to control the amount of light entering a room. These products are durable, easy to clean, and available in a variety of colors and finishes, making them a popular choice for both residential and commercial applications.
Potential applications and innovations: As technology continues to advance, the potential applications of plastic extrusion are expanding into new industries and areas. For example, the development of lightweight and high-strength plastic materials is opening up opportunities in the aerospace and automotive industries, where weight reduction is a critical factor. Additionally, the use of 3D printing technology in conjunction with plastic extrusion is enabling the production of complex and customized products with greater precision and efficiency. These innovations and emerging applications are expected to drive the growth of the plastic extrusion market in the coming years.
Challenges and opportunities in the industry: While the plastic extrusion industry offers numerous opportunities for growth and innovation, it also faces several challenges. One of the main challenges is addressing sustainability concerns, such as reducing plastic waste and developing more eco-friendly materials and processes. Additionally, the industry needs to adapt to changing market demands, such as the increasing demand for high-performance and customized products. However, these challenges also present opportunities for businesses to differentiate themselves by investing in research and development, adopting sustainable practices, and focusing on innovation to meet the evolving needs of the market.
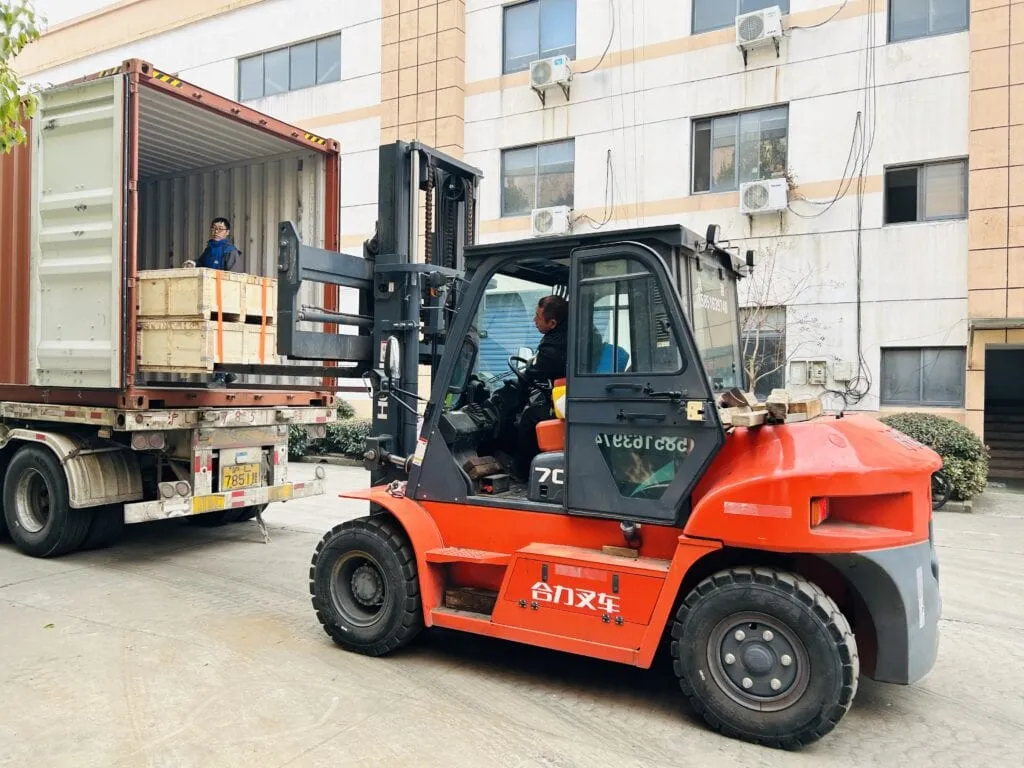
In conclusion, choosing the right extrusion line for plastic processing is crucial for achieving optimal efficiency and product quality. By considering factors such as material type, extruder selection, die design, temperature and pressure control,
and automation and control systems, manufacturers can set up an extrusion line that meets their specific production requirements. As the plastic extrusion industry continues to evolve, it is essential for businesses to stay updated with the latest trends and technologies, invest in regular maintenance and training, and focus on innovation to remain competitive in the market. We encourage readers to explore options for upgrading their extrusion equipment or consult with experts to find the best solution for their production needs, ensuring the continued success and growth of their plastic processing operations.