The bottled drinking water industry has grown exponentially over the past decade, driven by consumer demand for convenience and safe drinking water. For businesses looking to enter this lucrative market to set up a Mineral Water Plant, understanding the bottled mineral water production process is critical. This comprehensive guide explores the entire production workflow, from water treatment to packaging, with a special focus on advanced equipment like blowing-filling-capping 3 in 1 integrated machines that revolutionize efficiency.
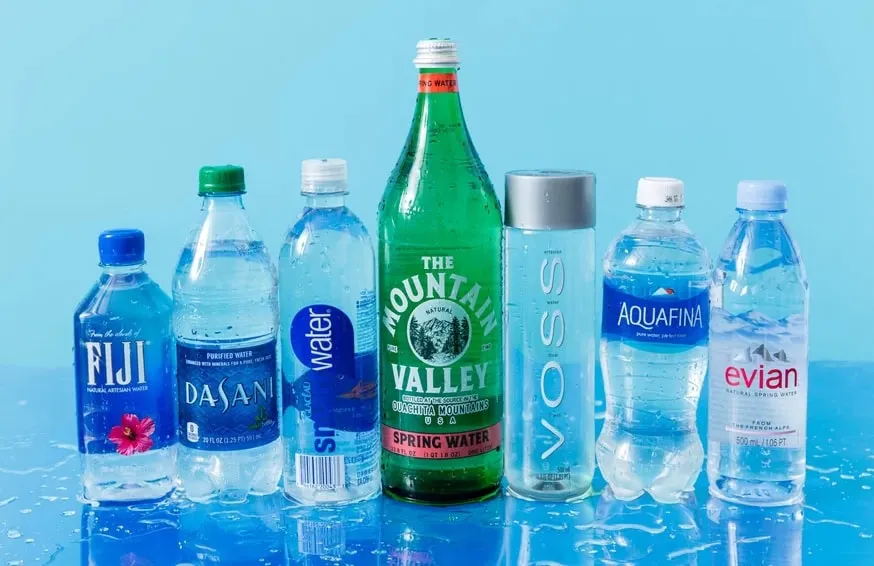
1. Overview of the Bottled Water Production Process
The production of bottled water involves four core stages:
- Water Sourcing and Treatment
- Bottle Manufacturing (Blow Molding)
- Filling and Capping
- Packaging and Labeling
Each stage relies on specialized machinery and stringent quality controls to ensure compliance with health standards and operational efficiency. Below, we break down these steps and highlight cutting-edge technologies that set modern production lines apart.
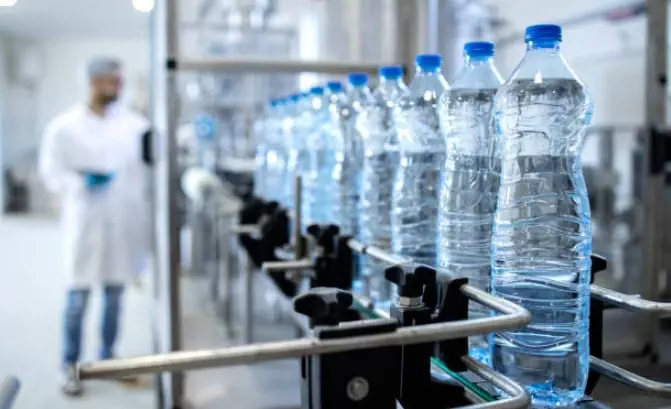
2. Water Treatment Equipment: Ensuring Purity and Safety
The foundation of any bottled water brand is the quality of its water. Whether sourced from natural springs, wells, or municipal supplies, raw water must undergo rigorous treatment to meet regulatory and consumer standards.
Key Water Treatment Steps
- Filtration: Multi-stage filters remove sediments, chlorine, and organic contaminants.
- Reverse Osmosis (RO): Removes dissolved salts, heavy metals, and microorganisms.
- UV Sterilization: Destroys bacteria and viruses without chemicals.
- Ozonation: Adds ozone gas to disinfect water and extend shelf life.
- Mineralization (Optional): Reintroduces minerals like calcium and magnesium for taste and health benefits.
Recommended Equipment:
- Reverse Osmosis Systems (e.g., Dow Filmtec membranes)
- UV Light Sterilizers (e.g., TrojanUV systems)
- Ozone Generators (e.g., Ozotech models)
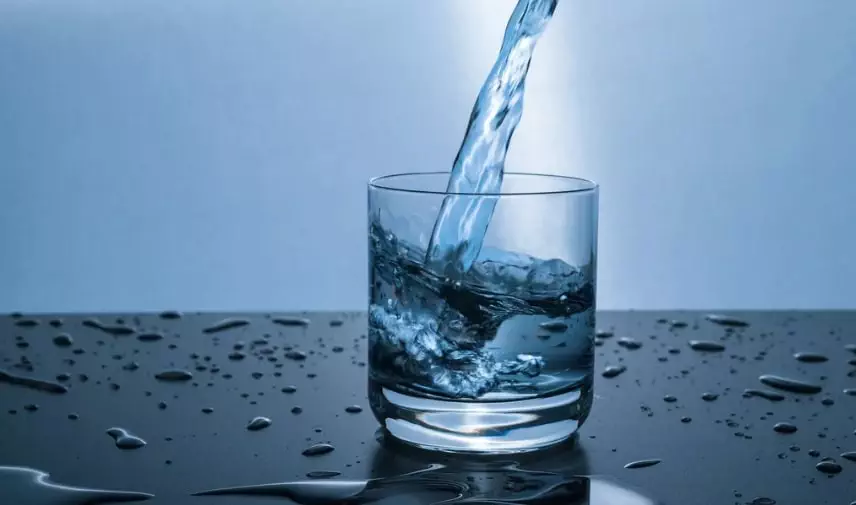
3. Bottle Manufacturing Equipment: Blow Molding Machines
The next step is creating the PET (polyethylene terephthalate) bottles that hold the water. This is achieved using bottle blowing machines, which blowing preforms into lightweight, durable bottles.
Types of Bottle Blowing Machines
- Injection Stretch Blow Molding Machine : Produces high-clarity, uniform bottles. Ideal for premium brands.
- Extrusion Blow Molding Machine: Cost-effective for larger containers but less precise.
How It Works:
- Preforms (tube-shaped PET blanks) are heated and placed into molds.
- Compressed air is injected, stretching the preform into the mold’s shape.
- The bottle cools and is ejected for quality checks.
Top Brands:
- Sidel: Renowned for high-speed ISBM machines.
- FaygoUnion: Offers energy-efficient models with IoT integration.
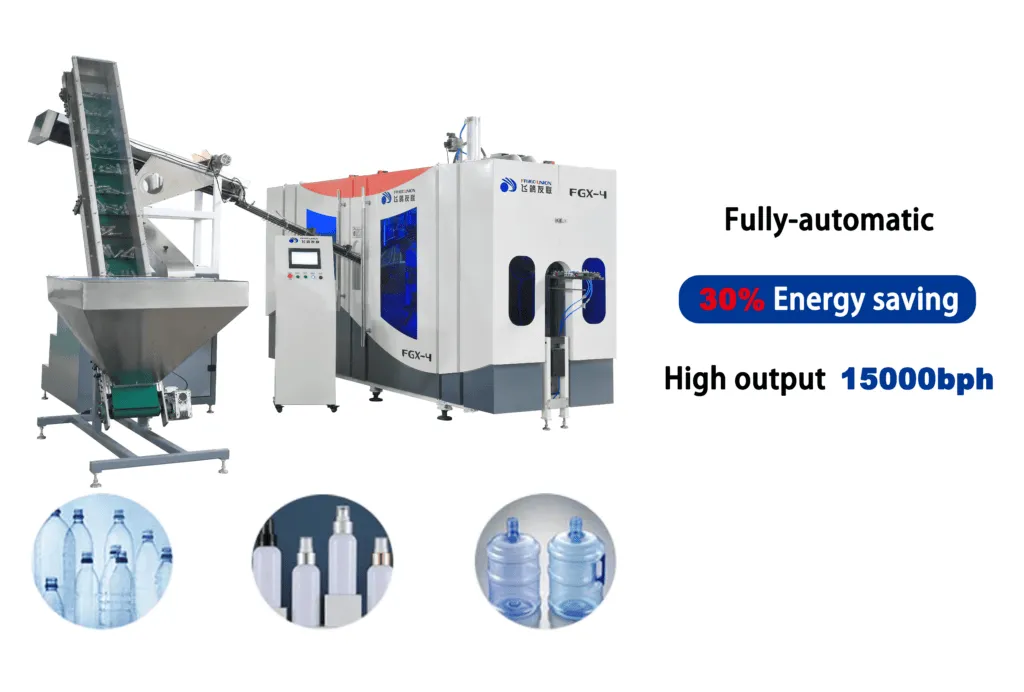
4. Filling and Capping Machine: Precision and Hygiene
Once bottles are formed, they move to the filling stage. Modern filling machines ensure accuracy and prevent contamination.
Filling Technologies
- Gravity Fillers: Simple, low-cost systems for still water.
- Piston Fillers: High-speed volumetric filling for carbonated water.
- Aseptic Fillers: Sterile environments for extended shelf life.
Capping Systems:
- Screw Cappers: For standard screw-top lids.
- Snap Cappers: For sports bottles with flip-top lids.
Leading Manufacturers:
- KHS Group: Modular fillers with CIP (Clean-in-Place) systems.
- Serac: Aseptic filling solutions for sensitive products.
5. The Game-Changer: Blowing-Filling-Capping 3 in 1 Integrated Machines
For businesses prioritizing efficiency and reducing contamination risks, blow-fill-seal integrated machines are a breakthrough. These systems combine bottle molding, filling, and capping into a single automated process.
Advantages of Blow-Fill-Seal Technology
- Space Savings: Eliminates separate machines for blowing, filling, and capping.
- Reduced Contamination: Seamless process minimizes human contact.
- Lower Operational Costs: 30–50% less energy and labor.
- Faster Production: 12000 to 72,000 bottles per hour.
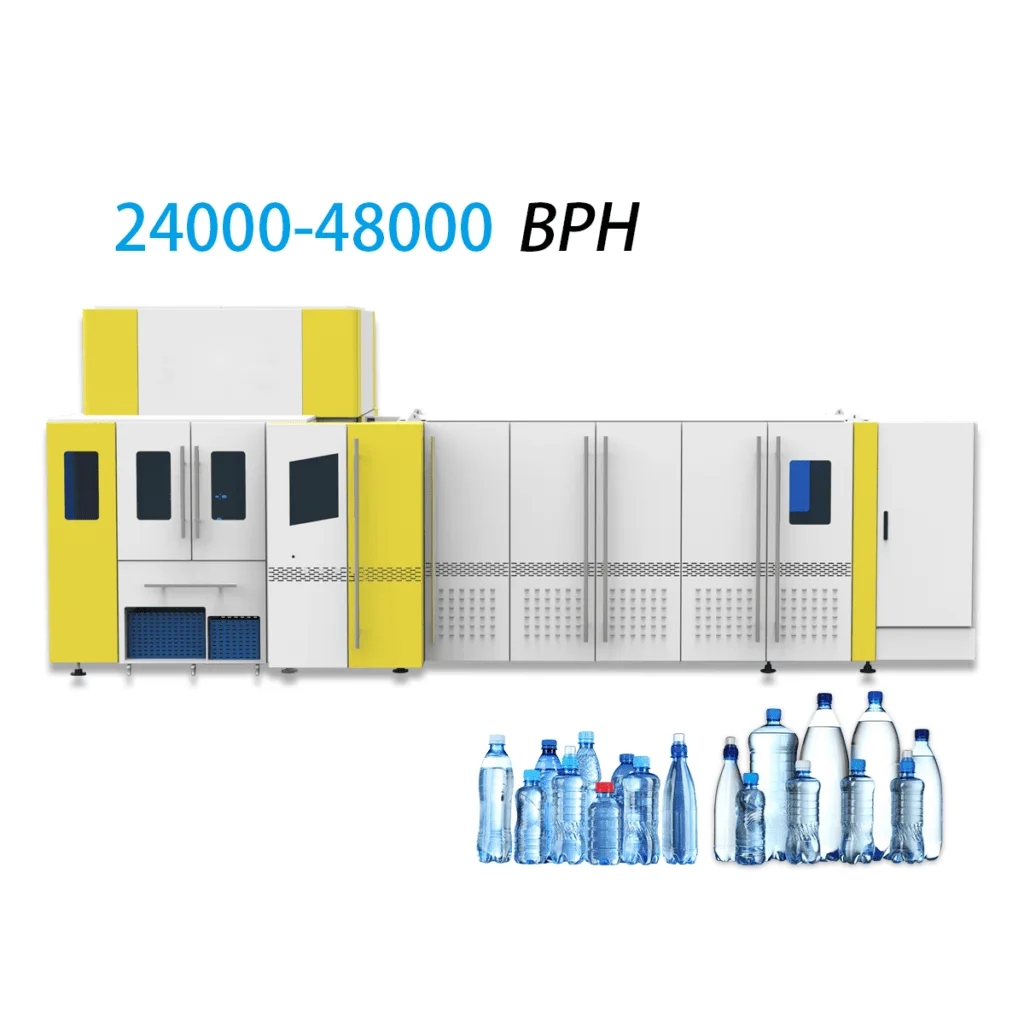
How It Works:
- PET granules are melted and extruded into a parison (hollow tube).
- The parison is blown into a mold, forming the bottle.
- Immediately, purified water is injected into the newly formed bottle.
- The bottle is sealed with a cap before ejection.
Top 3 in 1 Blowing Filling Capping Machine Manufacturers:
- Rommelag: Industry leader in aseptic BFS machines.
- FAYGOUNION: Compact systems for small to mid-sized producers.
6. Packaging and Labeling Machinery
The final stage involves packaging bottles into shrink wraps, cartons, or crates for distribution.
Key Equipment:
- Shrink Wrapping Machines: Use heat to apply plastic film.
- Case Packers: Automate bottle arrangement into boxes.
- Labeling Machines: Apply branded labels with QR codes or nutritional info.
Innovative Solutions:
- Krones’ Variopac Pro: Combines wrapping, boxing, and palletizing.
- Sidel’s Rollquattro Labeler: High-speed labeling for round and flat bottles.
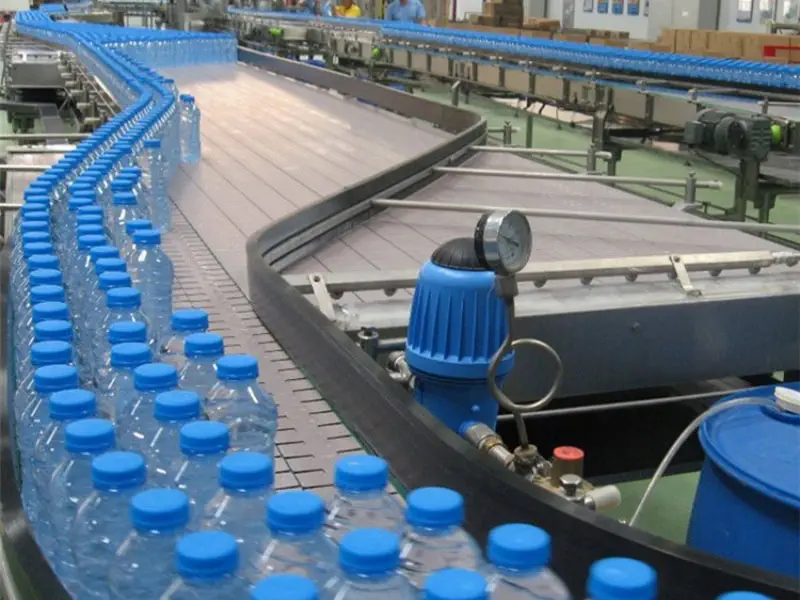
7. Quality Control and Sustainability Practices
Modern production lines integrate advanced sensors and AI-driven systems to monitor:
- Leak Detection: Laser sensors identify faulty seals.
- Weight Checks: Ensure consistent fill volumes.
- Material Recycling: PET scrap is reused to minimize waste.
8. Why Invest in Advanced Bottled Mineral Water Production Equipment?
Adopting technologies like blow-fill-seal integrated machines and IoT-enabled systems offers:
- Scalability: Easily adjust production volumes.
- Compliance: Meet FDA, EU, and WHO standards.
- Brand Reputation: Deliver consistent quality to build consumer trust.
Conclusion
The bottled water production process demands precision, hygiene, and cutting-edge equipment. From advanced water treatment systems to revolutionary blowing-filling-capping 3 in 1 machines, investing in the right technology ensures operational efficiency and product safety. For businesses aiming to dominate search rankings, optimizing content around keywords like “blow molding machines,” “bottled water filling systems,” and “blow-fill-seal technology” will attract targeted traffic and establish authority in this competitive industry.
By staying ahead with innovative solutions like integrated BFC systems, manufacturers can reduce costs, boost output, and meet the soaring global demand for bottled water.