Introduction to AMRs: Autonomous Mobile Robots
Autonomous Mobile Robots (AMRs) are intelligent machines designed to operate independently in dynamic environments. Unlike traditional industrial robots, AMRs stand out due to their ability to autonomously navigate and make real-time decisions, using advanced sensors and sophisticated software. These robots are highly versatile and can adapt to changes in their surroundings, making them ideal for applications in a variety of dynamic settings.
AMRs utilize a combination of sensors, artificial intelligence (AI), machine learning, and computing to plan paths and move efficiently around their environment. Unlike fixed transport industrial robots, AMRs can modify their routes as needed, providing greater flexibility and functionality for industries requiring agile automation solutions.
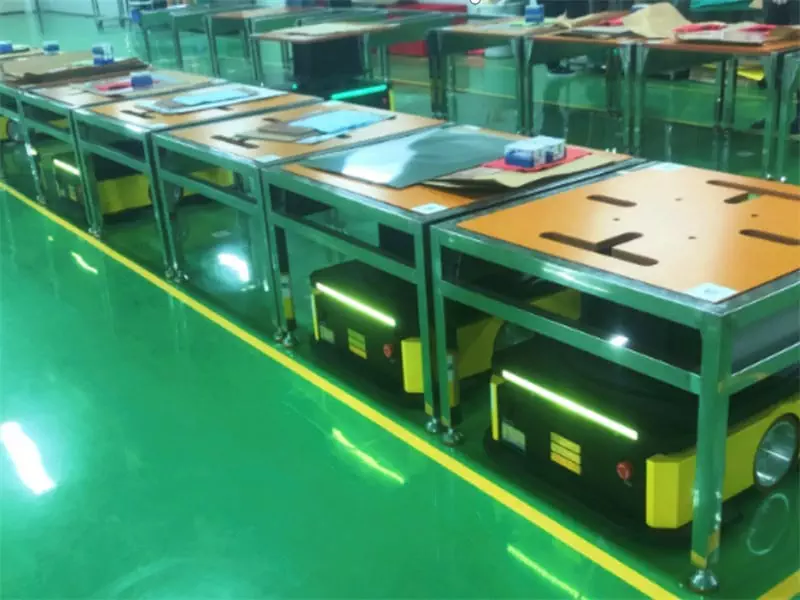
How Do AMRs Work?
At the core of an AMR is its ability to operate autonomously, meaning it can navigate and complete tasks without the need for human intervention. The integration of advanced sensors and intelligent software is what makes this possible.
AMRs rely on a complex array of sensors to determine their position, navigate obstacles, and adjust their movements. They use these sensors to understand their environment and identify obstacles in real time. The software that controls the AMR continuously analyzes this data to plan paths, modify routes, and ensure the robot reaches its destination efficiently.
AMRs can follow predefined routes or dynamically adapt their path as conditions change. For example, if an obstacle is detected, the AMR can autonomously find a new path to avoid it. In industrial settings, AMRs are often part of a larger fleet of robots, all controlled by a central software system. This software can schedule tasks, distribute duties, manage robot traffic, and even interface with more advanced systems for optimized operations.
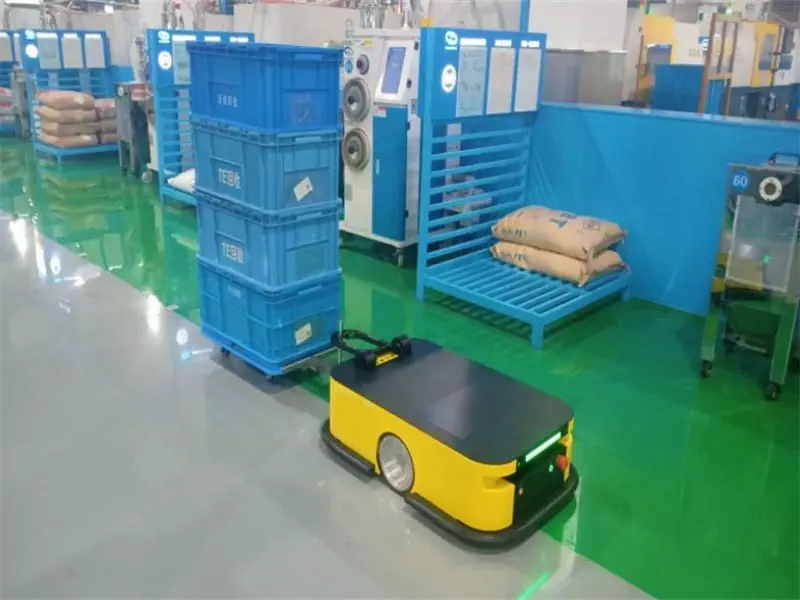
Benefits of AMRs in Industrial Automation
AMRs provide several advantages over traditional automation solutions, making them an attractive option for various industries. Key benefits include:
- Flexibility: AMRs can adapt to changes in their environment, allowing them to perform tasks that may require constant adjustments or dynamic re-routing.
- Collaboration with Humans: AMRs can work alongside human workers, enhancing productivity and reducing the workload for employees.
- Increased Efficiency: By performing repetitive tasks autonomously, AMRs free up human workers for more complex and creative tasks.
- Improved Accuracy and Consistency: AMRs offer greater precision and reliability in performing routine tasks, such as material handling or order fulfillment.
- Cost-Effectiveness: While the initial investment in AMRs can be high, their long-term cost-effectiveness is clear, thanks to their ability to operate 24/7 without breaks or fatigue.
Applications of AMRs
AMRs have found widespread use across various sectors due to their ability to adapt, work autonomously, and improve operational efficiency. Here are some of the most common applications:
- Warehousing and Logistics: AMRs are commonly used for order fulfillment, material handling, and inventory management in warehouses. They can autonomously transport goods and materials, increasing efficiency and reducing human labor costs.
- Healthcare: In hospitals and healthcare facilities, AMRs are used to transport medications, medical supplies, and patient records. They can access restricted or hazardous areas, enhancing safety and streamlining operations.
- Manufacturing: AMRs can deliver materials to production lines, assist with assembly tasks, or perform routine maintenance, thereby improving productivity and reducing downtime.
- Dangerous or Restricted Areas: AMRs are particularly useful in environments where human presence is risky, such as in nuclear plants, fire-fighting operations, or military settings. They can navigate hazardous environments autonomously, ensuring safety without human risk.
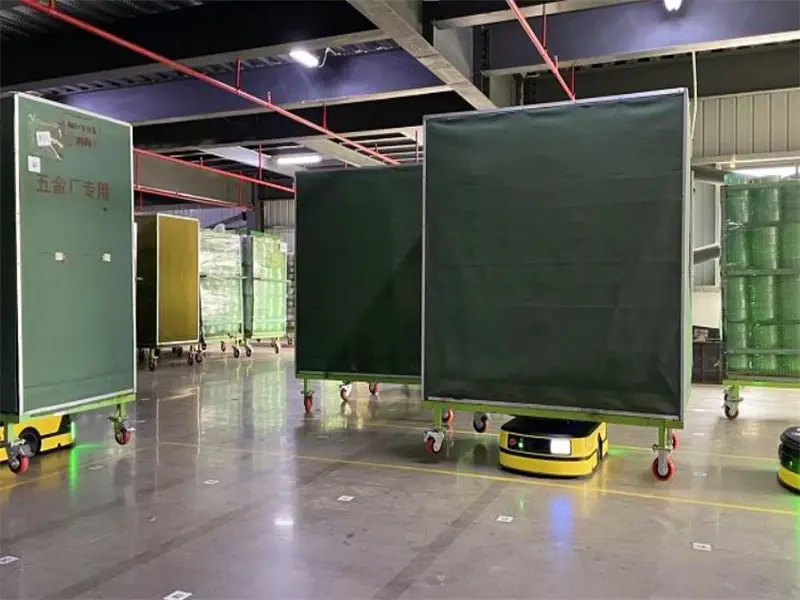
Comparison with Other Industrial Robots
While AMRs and Automated Guided Vehicles (AGVs) are often confused, there are significant differences between them.
- AMRs vs. AGVs: The key distinction between AMRs and AGVs is that AMRs are capable of autonomous navigation in dynamic environments, while AGVs typically follow predefined paths and are better suited for static, repetitive tasks. AMRs offer more flexibility, can navigate freely around obstacles, and adapt to changing conditions, whereas AGVs are more limited in their versatility and are typically used in controlled, predictable environments.
- Advantages of AMRs over AGVs: AMRs are more sophisticated, flexible, and cost-effective than AGVs, offering better adaptability and reduced infrastructure dependency. While AGVs work well for specific tasks in fixed environments, AMRs excel in environments where adaptability, mobility, and real-time decision-making are crucial.
Integrating AMRs with Other Systems
AMRs can be integrated with other systems to improve operational efficiency. A prime example of this is the integration of AMRs with the AutoStore automated storage and retrieval system (AS/RS). AMRs can transport target totes, racks, and bins from the AutoStore system, making it more flexible and adaptable compared to traditional AGVs. This integration allows warehouses to streamline their operations and improve space utilization, while increasing throughput.
AMRs can also be combined with other technologies, such as robotic arms or conveyors, to perform more complex tasks and further enhance automation.
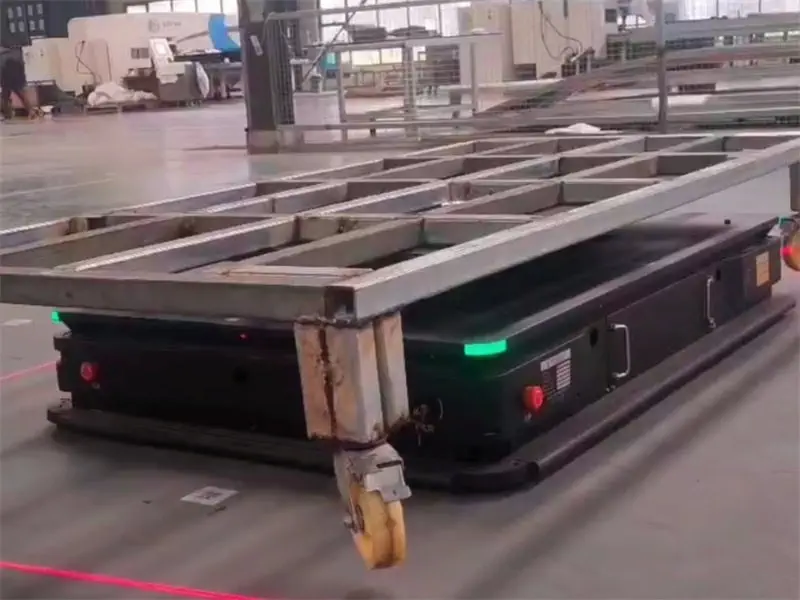
Challenges and Limitations of AMRs
While AMRs offer many benefits, they also come with their own set of challenges:
- Technical Challenges: Integrating AMRs with existing systems and infrastructure can be complex. Ensuring that AMRs work seamlessly with other automation systems requires careful planning and coordination.
- Operational Challenges: Developing and maintaining the software and algorithms that control AMRs is an ongoing challenge. The AI and machine learning algorithms used to navigate and plan paths must be continuously updated and optimized.
- Financial Challenges: The initial investment in AMRs and the infrastructure required for their deployment can be substantial. However, this is often offset by the long-term savings in labor and operational costs.
- Accuracy: While AMRs are highly efficient, they may face challenges in terms of precise location and positioning compared to AGVs, especially in complex environments.
Conclusion: The Future of AMRs
AMRs represent a significant leap forward in industrial automation. Their ability to navigate autonomously, adapt to changing environments, and work seamlessly alongside human workers makes them an invaluable tool across a range of industries. By understanding the technology behind AMRs and addressing the challenges involved, businesses can fully leverage these robots to improve efficiency, reduce costs, and drive innovation.
As AMRs continue to evolve, their role in industrial automation will only grow, bringing new opportunities for businesses to enhance their operations and stay ahead in an increasingly competitive market.
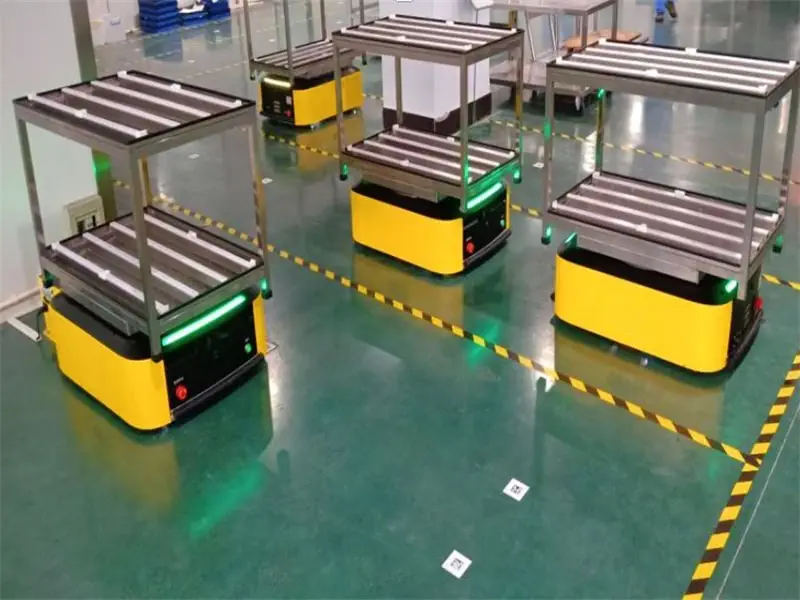