The extrusion process is a key manufacturing technique used across various industries, from automotive and construction to food and plastics. In this article, we’ll explore what extrusion is, its benefits, types, applications, and challenges. We’ll also delve into how businesses can leverage extrusion technology and plastic extruders to improve efficiency and production quality.
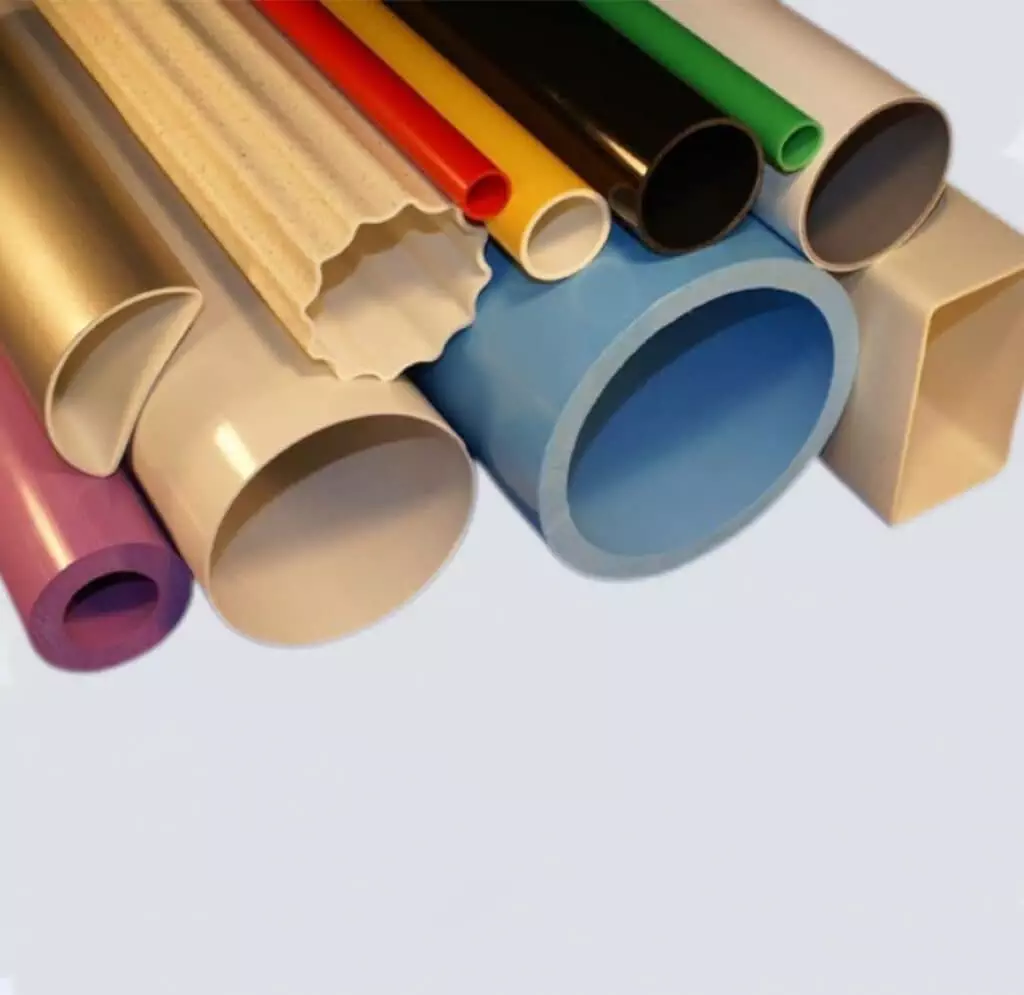
What is Extrusion process?
Extrusion is a manufacturing process in which raw material is forced through a die to produce an object with a fixed cross-sectional profile. The material is usually heated to a specific temperature to make it pliable, and then pushed or pulled through a mold to form continuous shapes. Once extruded, the material solidifies to retain its shape. Extrusion is widely used to create a range of everyday products in both the plastics and metals industries, making it a fundamental technique in modern manufacturing.
Extrusion is typically applied to metals, plastics, food, and ceramics. It is highly versatile, producing everything from pipes and window profiles to food packaging and medical products. Extrusion’s ability to create complex shapes in large volumes makes it a highly efficient and cost-effective process.
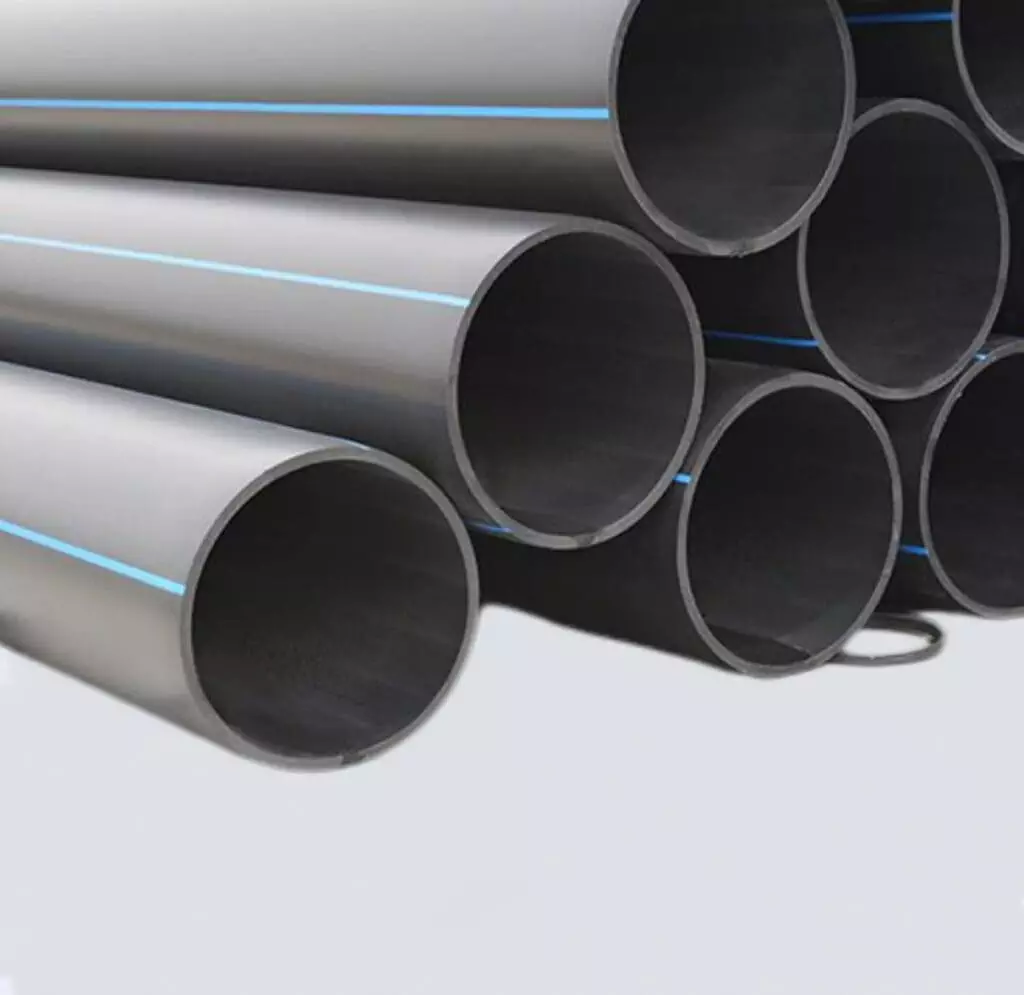
Types of Extrusion
There are several types of extrusion processes, each with specific capabilities suited for different materials and end products. Some of the most common types of extrusion are:
Direct Extrusion: This is the most widely used type of extrusion, where the material is pushed through a die. The material enters the extruder from a hopper and is forced through the die under pressure.
Indirect Extrusion: In this process, the die moves towards the material, rather than the material being pushed through the die. It is less common than direct extrusion but is used in certain specialized applications.
Cold Extrusion: This process is used for materials that do not require heating, such as some metals and plastics. Cold extrusion is typically used for materials that can maintain their strength and structure without the need for elevated temperatures.
Hot Extrusion: Hot extrusion involves heating the material before pushing it through the die. It is most commonly used in metal processing to create stronger and more durable products.
Co-Extrusion: Co-extrusion allows two or more different materials to be extruded simultaneously, resulting in multi-layered products. This is commonly used for products such as pipes, films, and sheets that require varying material properties for different layers.
Other Types of Extrusion: Other variations include hydrostatic extrusion, friction extrusion, and impact extrusion, which are employed for specialized purposes in different industries.
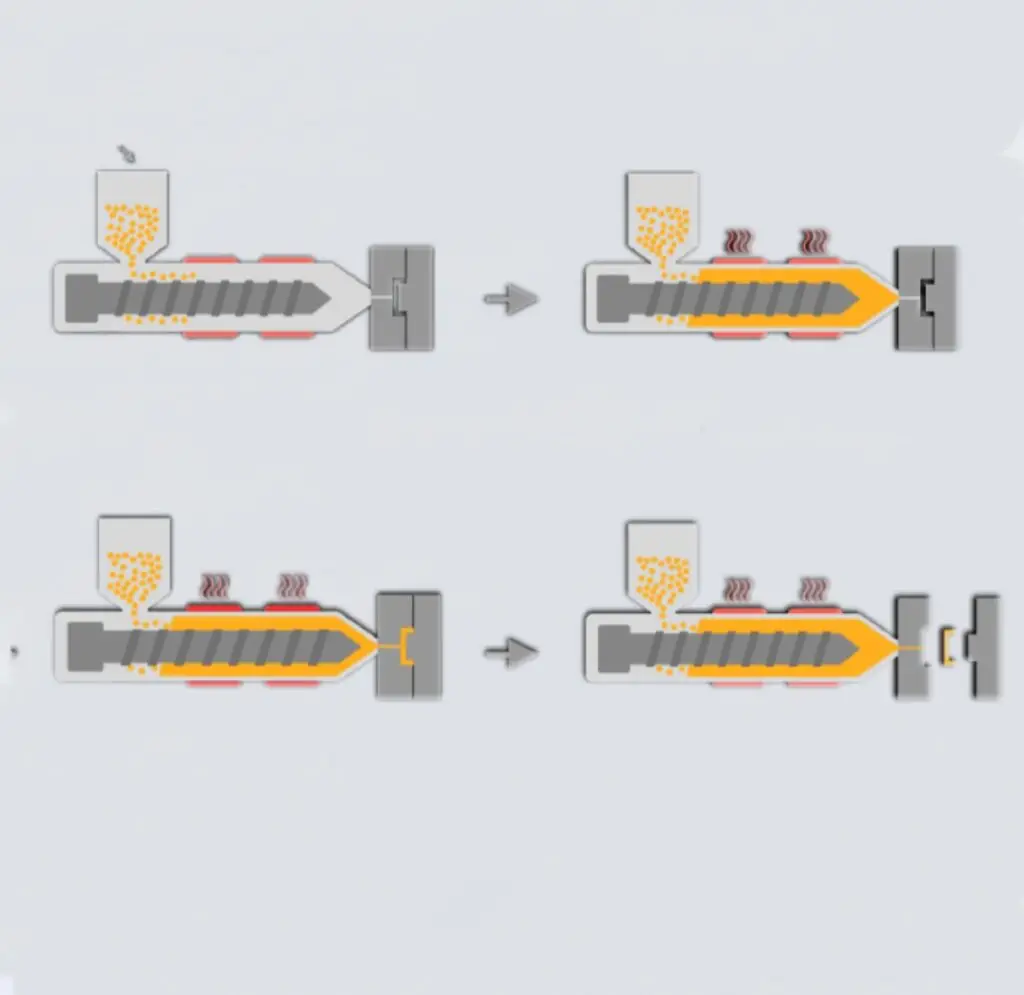
The Extrusion Process
The extrusion process generally follows several key stages:
Preparation of Raw Materials: The first step involves preparing the material. This can be plastic pellets, metal alloys, or even food products, depending on the intended output.
Heating: The material is then heated to a specific temperature that makes it soft and malleable. The temperature will vary depending on the material used.
Extrusion through a Die: Once the material is sufficiently heated, it is pushed or pulled through a die. The die shapes the material into the desired cross-sectional profile.
Cooling and Solidification: After passing through the die, the material is cooled to solidify its shape. Cooling is often achieved through water baths or air cooling, depending on the material and the type of extrusion process.
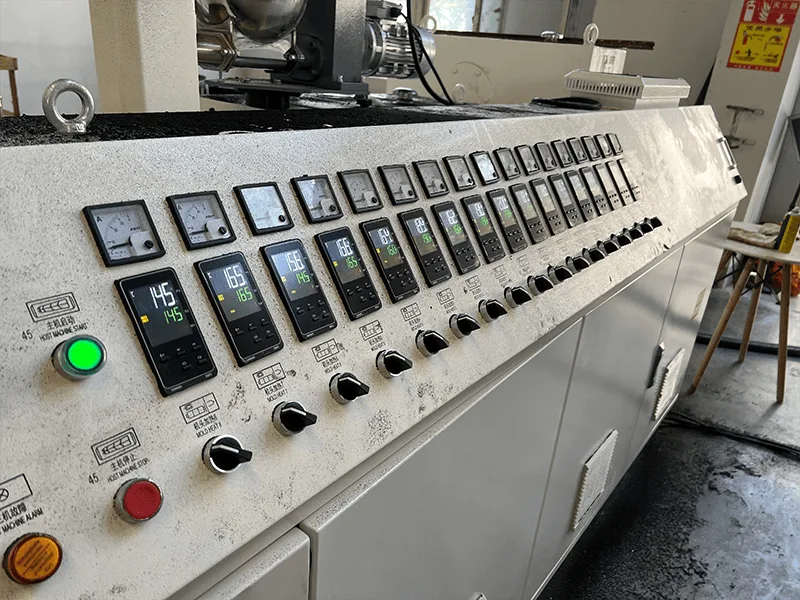
Applications of Extrusion
Extrusion is used across numerous industries to produce a wide variety of products. Some of the most common applications include:
1. Construction Industry
- Pipes and Tubing: Extrusion is commonly used to create pipes and tubing for water supply, gas lines, electrical conduits, and more. Plastic extrusion, in particular, is ideal for creating strong and durable pipes used in plumbing and irrigation systems.
- Window and Door Profiles: Extrusion is also used to produce custom window and door profiles, particularly in PVC, which is weather-resistant and energy-efficient.
2. Automotive Industry
- Custom Automotive Parts: Plastic extrusion plays a crucial role in producing lightweight automotive components such as bumpers, fluid hoses, and wiring harnesses. These products benefit from the strength, durability, and light weight of extruded plastics, helping to reduce the overall vehicle weight.
3. Packaging Industry
- Flexible and Rigid Packaging: Extrusion is used to create packaging materials such as flexible films, rigid containers, and protective materials like bubble wrap. This process allows manufacturers to produce large volumes of packaging that meets exact specifications for consistency and quality.
4. Medical and Food Industries
- Medical Tubing: Medical applications often require sterile, high-quality tubing. Extrusion processes are used to create custom tubing for medical devices.
- Food Packaging: The food industry uses extrusion to create packaging products like containers and wraps that are safe and efficient for preserving and distributing food.
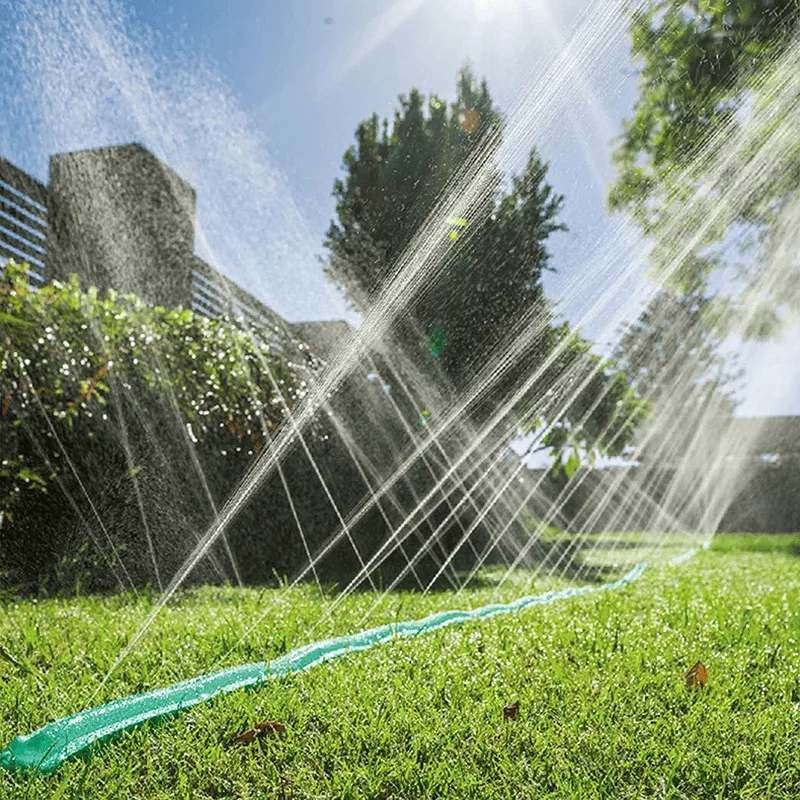
Benefits of the Extrusion Process
The extrusion process offers a range of benefits that make it a preferred manufacturing method in various industries:
- Efficiency: Extrusion can produce large volumes of material continuously, reducing production times and costs.
- Versatility: The extrusion process is highly versatile and can be applied to a wide variety of materials, including metals, plastics, food, and more.
- Cost-Effectiveness: Extrusion minimizes waste and reduces labor costs compared to other manufacturing methods.
- Customization: Extrusion allows for precise control over the material properties, such as thickness, density, and texture, making it ideal for custom products.
The Role of Extruder Machines in Manufacturing
Extruder machines are at the heart of the extrusion process. These machines consist of several key components:
- Hopper: This is where the raw material is fed into the extruder machine.
- Screw: The screw pushes the material through the barrel, creating the necessary pressure and heat for extrusion.
- Barrel: The barrel houses the screw and helps maintain the temperature needed for extrusion.
- Die: The die shapes the material into the desired profile.
- Cooling System: Once the material has been extruded, it must be cooled to maintain its shape.
Plastic extruder machines are essential for ensuring product consistency, quality, and precision. They play a crucial role in creating uniform, high-quality products across industries like packaging, construction, and automotive.
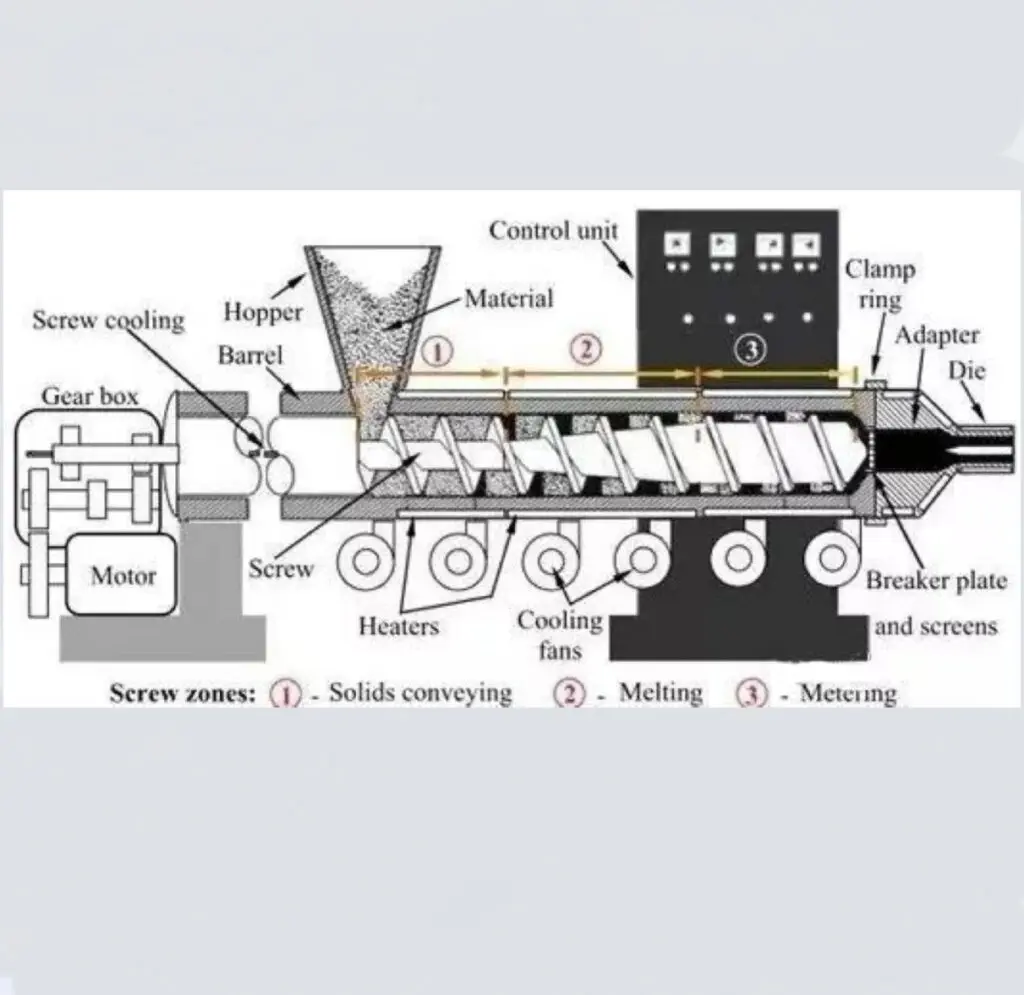
Common Challenges in the Extrusion Process
Despite its advantages, the extrusion process can face challenges:
- Material Blockages: Incorrect material selection or improper temperature settings can lead to material blockages, slowing down production.
- Inconsistent Product Quality: Variations in machine calibration or improper maintenance can lead to defects in the final product.
- Energy Consumption: Extrusion processes can be energy-intensive, especially when dealing with large volumes of material.
- Equipment Wear and Tear: Regular maintenance is necessary to prevent wear and tear on extruder machines, which can affect production efficiency.
Conclusion
Extrusion is a vital manufacturing process used across a wide range of industries. From producing pipes for construction to creating custom automotive parts, extrusion offers a cost-effective, efficient, and versatile solution for many different applications. By investing in advanced extruder machines, businesses can improve production quality and reduce operational costs.
If you’re looking to optimize your manufacturing processes and ensure high-quality output, consider the advantages of modern extrusion technology. Whether you’re in the packaging, construction, automotive, or medical industries, understanding and investing in extrusion processes and equipment is essential for staying competitive.
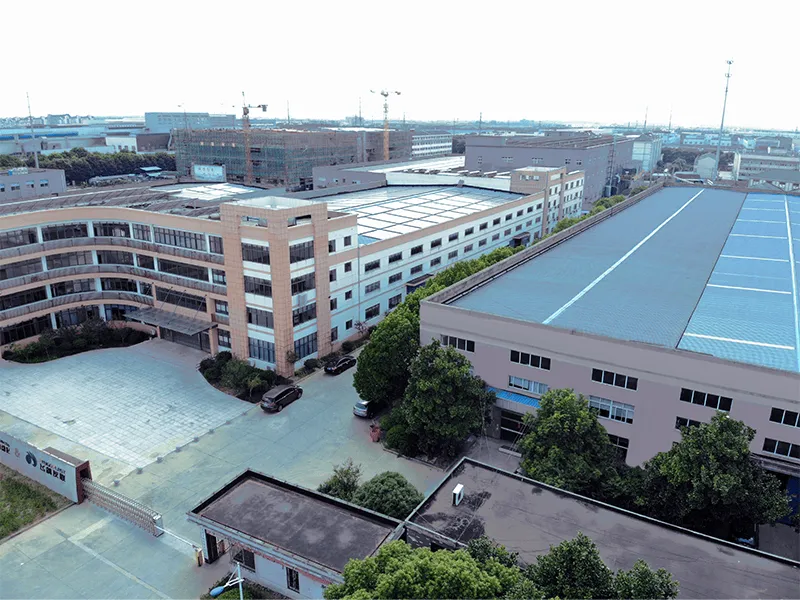
At FAYGO UNION, we specialize in providing high-quality plastic extruder machines designed to meet the specific needs of your business. Our state-of-the-art extrusion machines ensure consistent product quality, efficiency, and cost-effectiveness. Whether you’re looking to produce flexible packaging, automotive parts, or custom medical tubing, our machines are engineered to meet your exact specifications.
Ready to enhance your manufacturing processes with precision and efficiency? Contact us today to learn more about our advanced plastic extruder machines and how they can help you optimize production.