Selecting the perfect plastic extrusion line is critical to achieving superior manufacturing outcomes and maintaining consistent product quality. At Faygo Union, we recognize that the right equipment can significantly impact efficiency and production standards. This guide highlights seven crucial factors to help you make an informed decision tailored to your manufacturing needs.
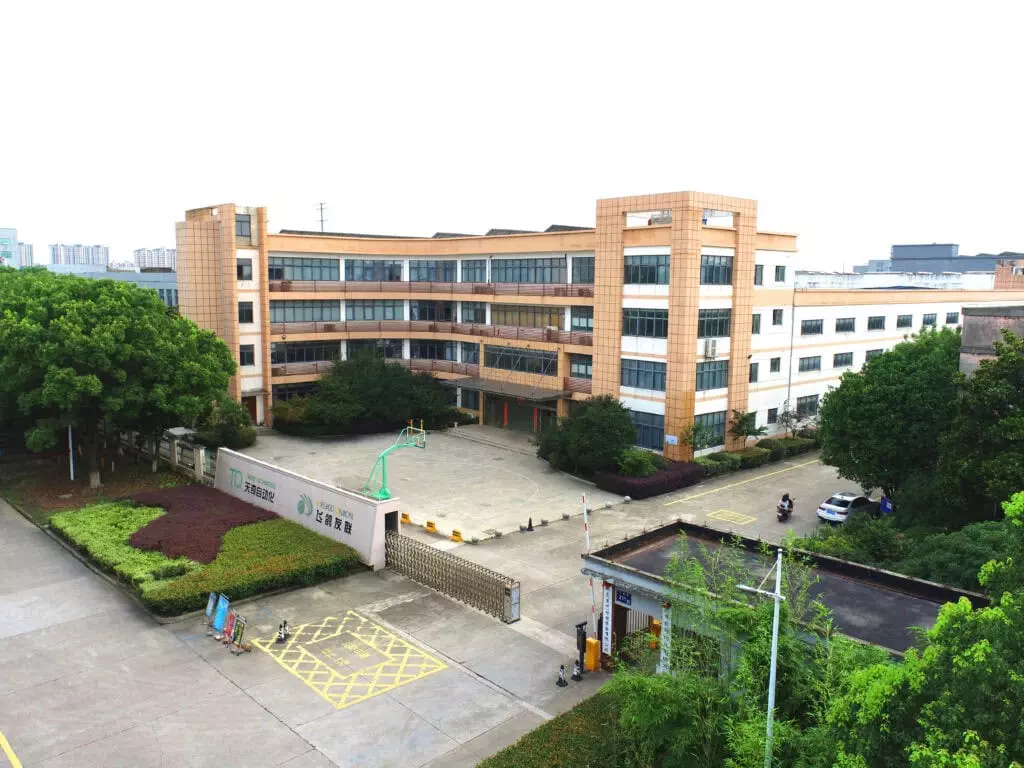
Understanding the Plastic Extrusion Line: Process and Applications
What is Plastic Extrusion?
Plastic extrusion is a versatile manufacturing technique designed to produce high volumes of items like pipes, sheets, and profiles. This continuous process involves heating plastic materials and shaping them into uniform cross-sectional forms, making it ideal for applications in industries such as construction, automotive, and packaging.
What is a Plastic Extrusion Line?
A plastic extrusion line integrates key components like an extruder, die, cooling system, puller, and winder to create finished products with precision. Faygo Union’s extrusion lines are engineered for reliability, speed, and adaptability to meet diverse industrial requirements.
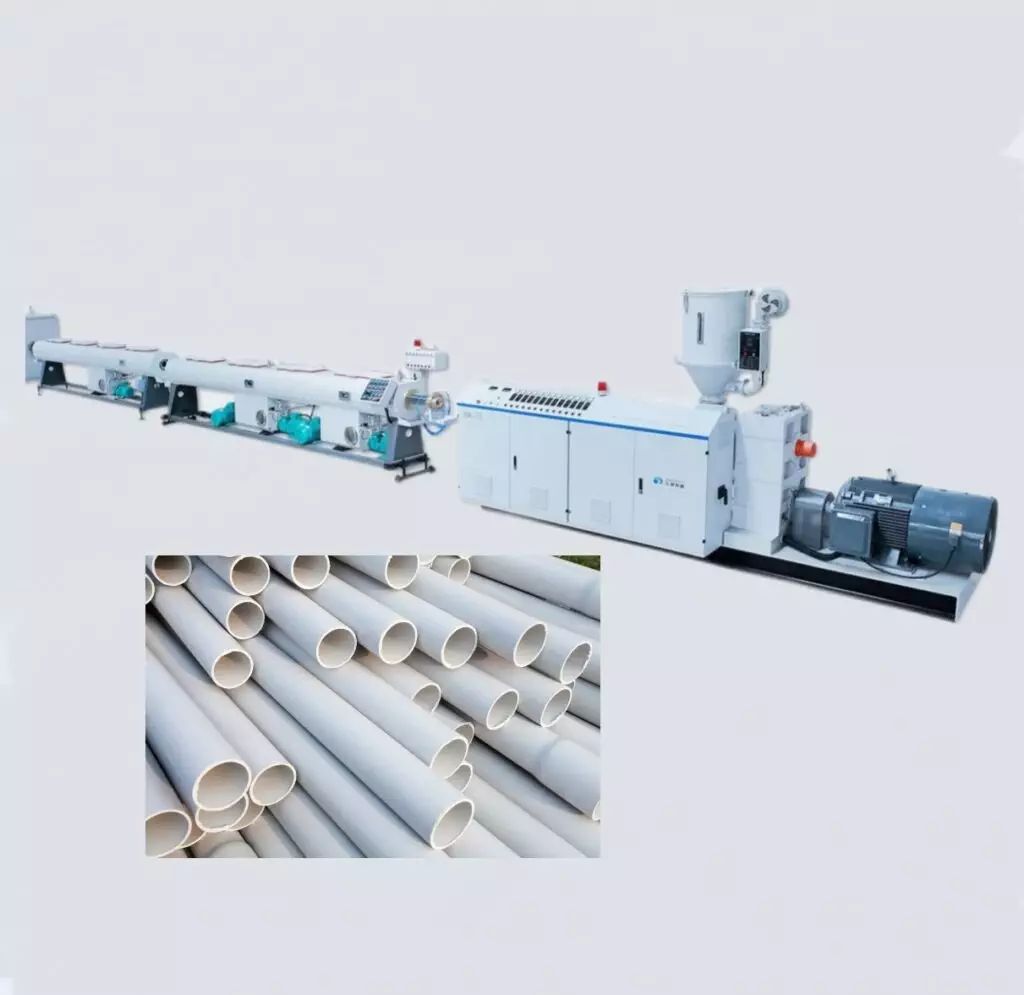
1. Define Your Product Specifications
Every product demands specific production capabilities:
- Plastic pipe lines: Designed for infrastructure projects needing durable and standardized piping systems.
- Plastic sheet production lines: Suited for creating smooth, uniform sheets utilized in packaging or automotive industries.
- Profile extrusion lines: Ideal for manufacturing intricate shapes like window frames or sealing profiles.
Understanding your product’s unique requirements ensures you select machinery that aligns with your goals.
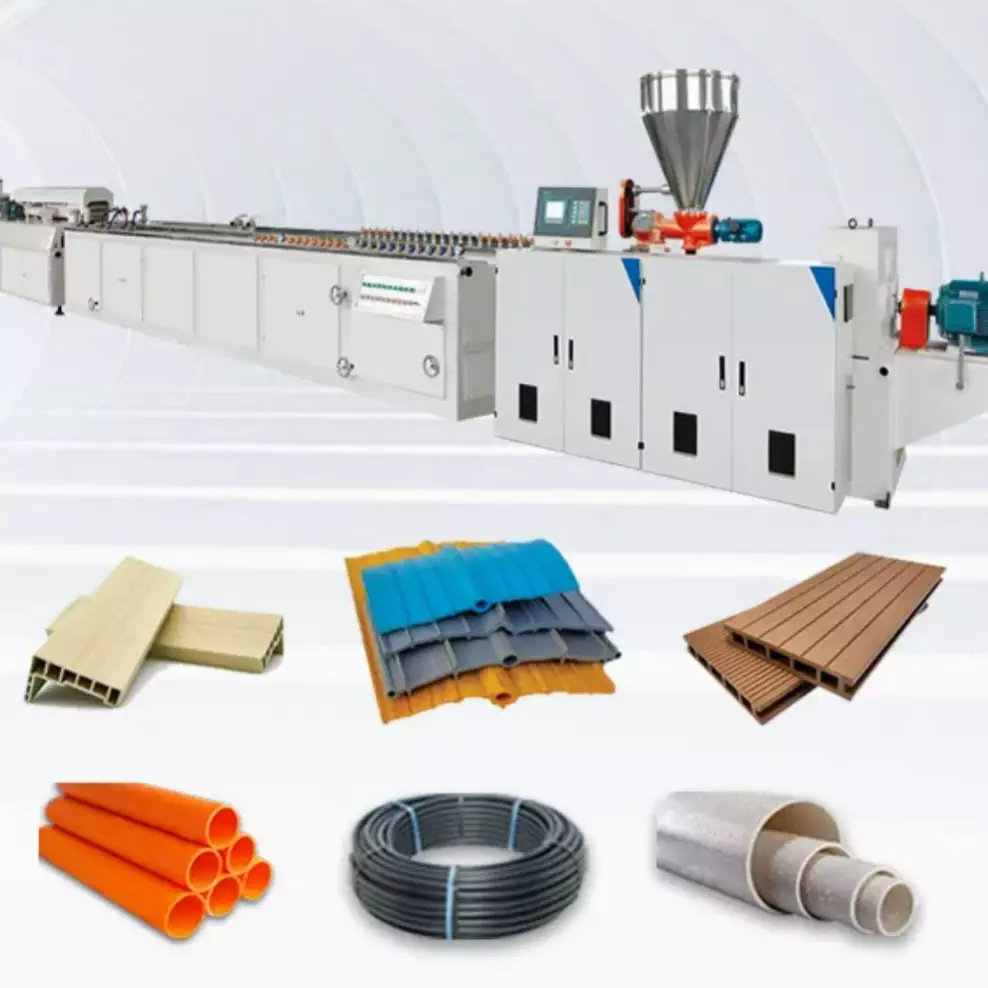
2. Focus on Material Compatibility
The type of material you plan to process is pivotal in choosing the right extrusion line. Faygo Union’s machines are compatible with a wide array of plastics, such as:
- PVC: Commonly used for rigid pipes and profiles.
- Polyethylene and Polypropylene: Preferred for flexible films, tubing, and packaging materials.
- ABS and Polycarbonate: Best for high-strength and impact-resistant products.
Matching your extrusion line to the material ensures product integrity and consistency throughout production.
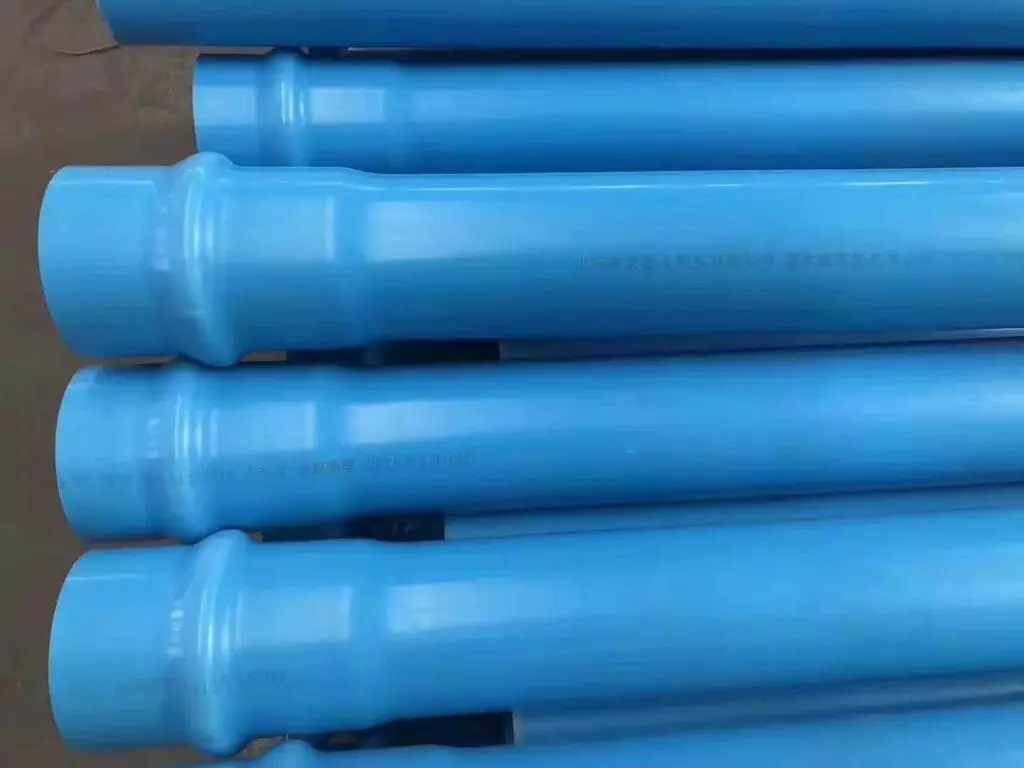
3. Select the Right Extruder Type
Choosing between a single-screw and twin-screw extruder depends on your application:
- Single-screw extruders: Cost-efficient, simple to operate, and ideal for straightforward shapes like sheets and pipes.
- Twin-screw extruders: Deliver better mixing, higher output speeds, and improved performance for complex designs or multi-layered products.
Faygo Union’s extruders are crafted for efficiency, durability, and precision, ensuring excellent results for various applications.
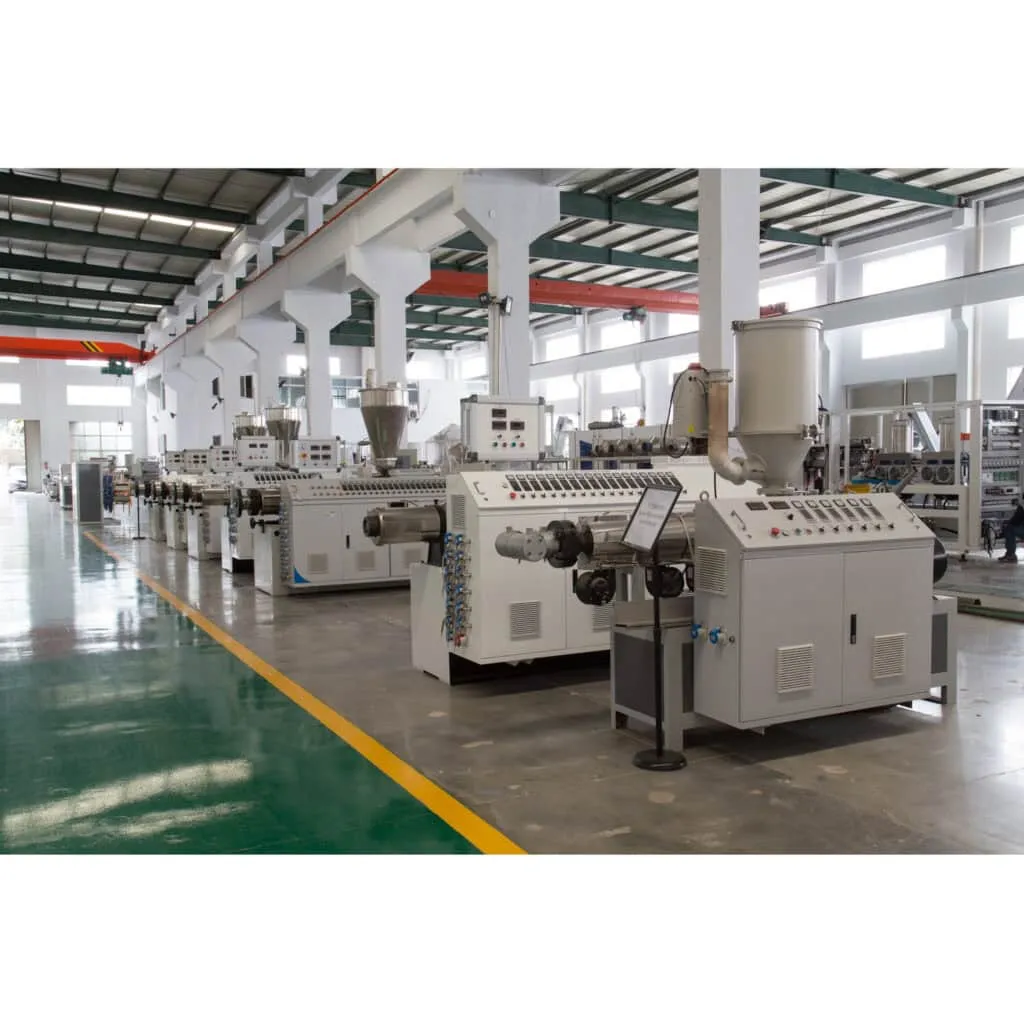
4. Evaluate Energy Efficiency
Energy costs account for a substantial portion of operational expenses. Faygo Union incorporates cutting-edge energy-saving technologies into our extrusion lines, including high-efficiency motors, precise temperature controls, and optimized heating systems. These features not only lower operational costs but also reduce environmental impact.
5. Adopt Smart Technology and Automation
Modern manufacturing demands intelligent automation. Faygo Union’s advanced extrusion lines integrate features such as automated feeding systems, AI-driven monitoring, and precision control systems. These innovations improve operational efficiency, enhance product consistency, and reduce waste, making them indispensable for competitive production.
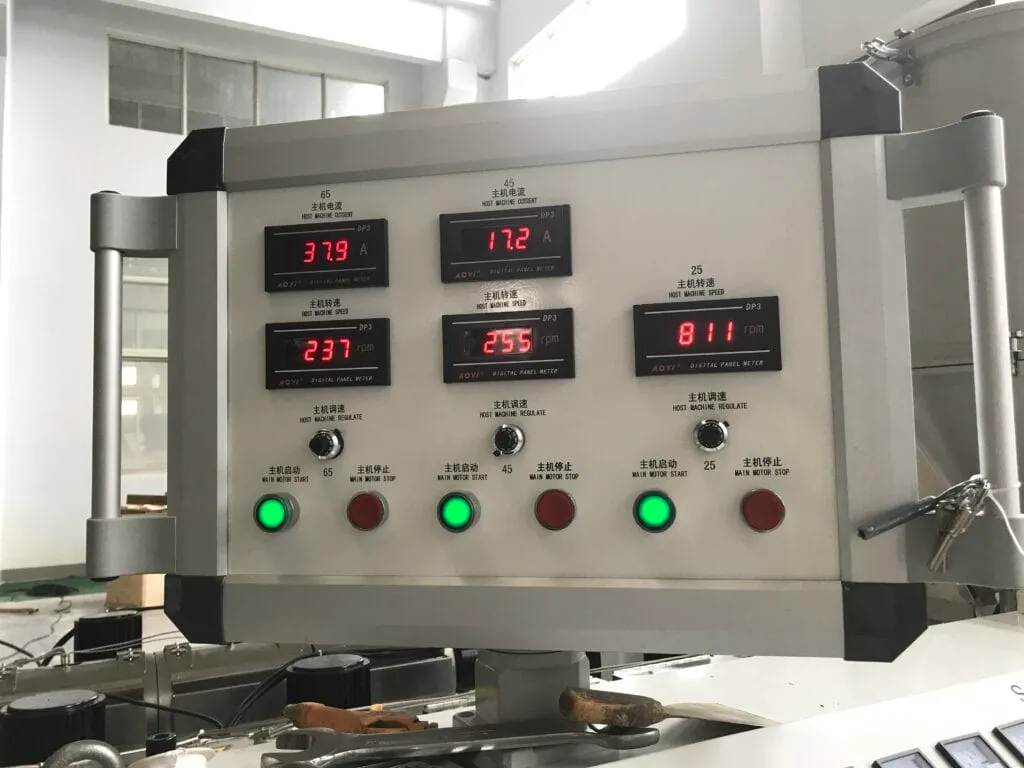
6. Seek Flexibility and Customization Options
Adaptability is key in a competitive market. Faygo Union offers tailored solutions, such as adjustable die systems and specialized cooling configurations, to accommodate diverse product specifications. Customization ensures your machinery evolves with changing production demands.
7. Assess Maintenance and Support Services
Reliable after-sales support and easy access to spare parts are crucial for uninterrupted production. Faygo Union prioritizes service excellence with durable machines designed for reduced maintenance needs and a responsive technical support team to address any challenges.
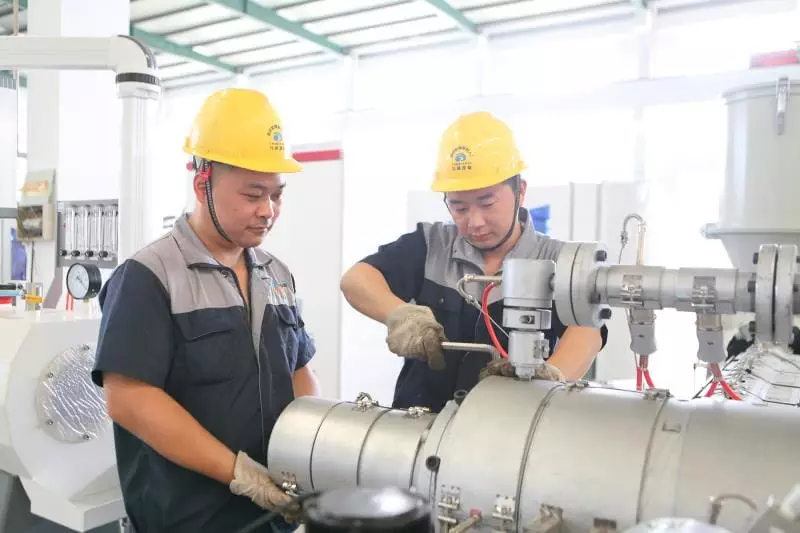
Conclusion
Making an informed decision when selecting a plastic extrusion line can elevate your manufacturing processes, improve efficiency, and ensure consistent quality. By addressing key factors like product requirements, material compatibility, and energy efficiency, you can optimize your extrusion plastic manufacturing process and gain a competitive edge.
At Faygo Union, we are passionate about delivering top-tier extrusion solutions. Our state-of-the-art 35,000-square-meter facility and a team of over 200 skilled professionals reflect over two decades of expertise in manufacturing high-speed PET bottling lines and advanced extrusion technologies.

Ready to enhance your production capabilities? Contact Faygo Union today for expert guidance on selecting the perfect extrusion line tailored to your specific needs.